In the age of Industry 4.0, industrial digital transformation, and Logistics 4.0, supply chain management is becoming ‘smart’. However, the digital, connected and smart supply chain is far from a fact yet, as is supply chain visibility and collaboration.
Between realizing the industrial and supply chain transformation goals of what often has been called the smart supply chain, smart industry and smart manufacturing, as envisioned in Industry 4.0 and Industrial IoT on one hand, and the reality in manufacturing and of actual supply chain visibility and collaboration on the other, are different challenges.
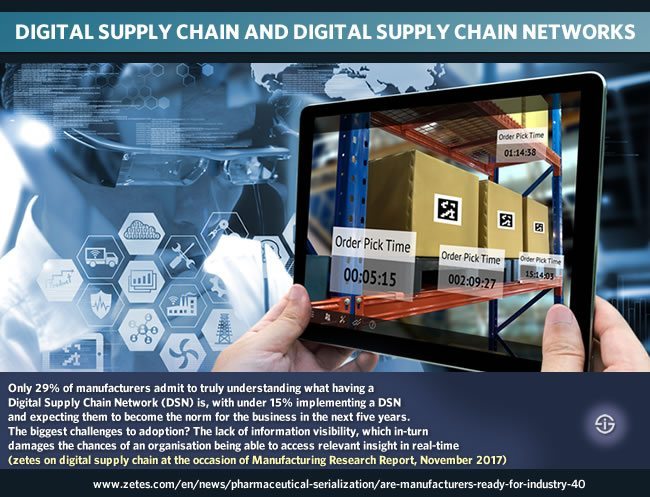
As written before there is still quite a lot of paper moving around in manufacturing and information sharing across the supply chain happens through good old email, EDI and fax, far from digital supply networks. In other words: the end-to-end smart chain with seamless information flows, let alone easy and fast access to critical information, de facto is far away for many.
Information silos and disconnects, legacy issues and other factors standing in the way of supply chain visibility and collaboration
While IoT and cyber-physical systems, joined by all those other existing (yet changing) and new manufacturing technologies, are increasingly being adopted and the digital transformation of manufacturing increasingly goes hand in hand with the usage of IoT in manufacturing, the truth about the state of smart and digital supply chains and the ability to enhance supply chain visibility and collaboration, with a key role for information sharing capabilities and processes, is different.
If you look at the essence of Industry 4.0, the Internet of Things and the digital economy overall it’s clear that information is critical in all aspects. The ability to leverage it for any given purpose and to connect and share the meaningful intelligence and insights from it with various key stakeholders within the supply chain is equally important.
Yet, just as paper, information silos and disconnects on all levels of information slow down digital transformation strategy, prevent staff from doing their job efficiently, lead to underwhelming customer experiences and stand in the way of the types of information aggregation and exchanges that enable organizations to do better and even innovate in all industries and sectors, the exact same thing obviously is true for manufacturing and the supply chain.
Manufacturers know that across the industry there needs to be greater focus on speed, accuracy and agility within the end-to-end supply chain, if they are to remain competitive and achieve the nirvana of Industry 4.0 (Sébastien Sliski)
It is an old, yet persistent, problem that has many reasons and shows in many ways, depending on industry and type of business: the disconnect between back office and front-end, legacy systems, culture and even the recognition of the importance of information.
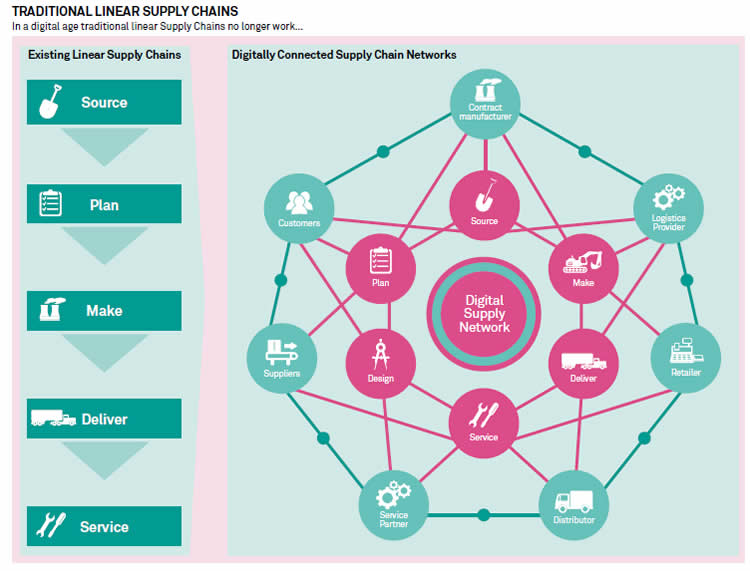
The state of the digital supply chain – and of digital supply networks
It shouldn’t really come as a surprise that many manufacturers aren’t ready for Industry 4.0, let alone for the realization of a digital supply chain when taking all these factors into account.
Once more reminding that the challenge is not just one of manufacturing, we get a look at the state of the digital supply chain, digital supply networks and supply chain visibility and collaboration in a November 2017 report by Sapio Research on behalf of Zetes. It is based upon a survey of 330 senior managers within a range of manufacturing sectors across Europe and South Africa. The report shows how a lack of end-to-end supply chain visibility and even access to information to make business decisions stand in the way of the goals of manufacturers.
At present, manufacturers state securing meaningful intelligence from their end-to-end supply chain as a challenge (80%), dealing with-real time information (75%) and the ability to deal with the intelligence – as significant hurdles that need to be overcome (Zetes)
While the survey shows that manufacturers want to improve supply chain visibility and collaboration, increase agility, mitigate risk, be more efficient and respond to legislation, they have a hard time to deliver upon customer promises and respond to customer demands in today’s more complex and demand-driven manufacturing environment where end-to-end control, real-time visibility and agile process execution are among many priorities.
However, in order to achieve this, the research confirms, seamless collaboration, supported by efficient processes and real-time information exchange at every step, are needed. Yet, the majority of manufacturers is not able to achieve this.
While 89 percent of responding manufacturers perceive a single view of the supply chain as a key priority, 70 percent have no end-to-end visibility.
There also seems to be a poor understanding of a digital supply network (note: not exactly the same as a digital supply chai,n which in this scope aims the enablement of insights and higher efficiency by being better able to get the right people, resources and information where they are needed at the right time and place in a connected context).
According to the survey only 29 percent of manufacturers admit that they really understand what having a digital supply network (DSN) is. Less than 15 percent of respondents is implementing a digital supply network and expecting DSNs to become the norm for the business in the next 5 years, as you can read in the announcement where there are also more findings from the survey.
The struggle of access to the right information for business decisions and supply chain information sharing
More worrying is that 68 percent of responding manufacturing decision makers state they don’t have access to the right information and insights to make informed business decisions and that 67 percent are struggling to share key information between/with their suppliers, partners and even their own departments.
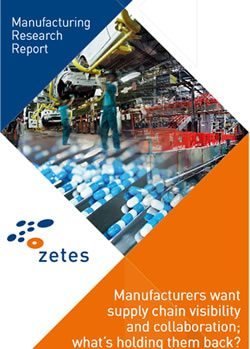
Just as the challenges have a lot to do with information and the ability and processes to leverage it in an environment where dealing with real-time information becomes critical, the solutions are about information, processes and the ability to derive meaningful insights from real-time data sources and streamlined information flows – and the ways of sharing those with key supply chain stakeholders – as well.
To quote Sébastien Sliski, General Manager Supply Chain Solutions at Zetes: “Manufacturers know that across the industry there needs to be greater focus on speed, accuracy and agility within the end-to-end supply chain, if they are to remain competitive and achieve the nirvana of Industry 4.0. The only way they are going to be able to reach such heights is to optimize processes between legacy and new systems as well as providing key stakeholders with meaningful insight from real-time data sources”.
Top image: Shutterstock – Copyright: Zapp2Photo – All other images are the property of their respective mentioned owners.