Although the concept of digital twins isn’t new and exists since before the term digital twin was coined at the start of this Millennium, it took until this decade before digital twin technology, the various digital twin use cases and the potential benefits gained more attention.
In an Industrial IoT context digital twin usage grows fast a 2018 Gartner digital twin report finds, offering digital twin best practices for CIOs on top of data regarding (planned) usage.
First, quickly back to the digital twin roots to understand today’s evolutions and impact. On top of the possibilities and several ways to create value which digital twins offer (whereby there is still a lot to explore and try on multiple levels; products, assets and beyond) as a driver of the rise of digital twins in industrial applications, there are several key technology-related drivers. The latter overlap with the factors that contributed to growing adoption of the Internet of Things (initially in the enterprise and Industrial IoT segments), the acceleration of digital transformation and the evolutions enabling Industry 4.0.
Think about cheaper and smarter sensors, (big) data and advanced data analytics, changes on the level of connectivity (more, cheaper, mobile, ubiquitous), in the scope of digital twins of course the visualization and user interface technologies (e.g. VR/VR, voice interfaces, 3D CAD and far more, depending on digital twin use case), and last but not least, IoT which includes a lot of the above and brings along faster integration of IT and OT.
Add edge computing and AI engines and machine learning and you have pretty much all of the components of today’s advanced integrated Industrial IoT deployments and a big chunk of the backbone of many digital twin initiatives.
Especially in the period 2014-2016 digital twin technology started getting increasing attention. This timing isn’t a coincidence given some of the mentioned enablers. Look at the ‘history’ of Industry 4.0 and what GE first called the Industrial Internet and the parallels are clear (as are the names of the leading companies).
Gartner digital twin forecasts: the use or intended use of digital twins is high for organizations with IoT
There is an acceleration with regards to Industrial IoT digital twin initiatives. In a previous article on the digital twin market evolutions we cited Gartner digital twin forecasts.
Gartner predicted that by 2021, half of large industrial companies would use digital twins as the research firm added digital twin to its Top 10 Strategic Technology Trends for 2018 (as it did the year before), with especially “digital twins in the context of IoT projects being particularly promising over the next three to five years”.
Gartner announced another digital twin report in March 2018, offering digital twin initiative advice in the form of four best practices for CIOs on top of the mentioned (and more) additional findings about the evolutions. Already having said that “digital twins in the context of IoT projects lead the interest in digital twins today”, Gartner zoomed in on the plans of organizations which implemented IoT on the level of digital twins.
A key finding: of all respondents to the Gartner IoT implementation survey leading to the findings and carried out across China, the US, Germany and Japan, 48 percent of those respondents which are active in organizations that are implementing IoT either 1) already used or 2) intended to use digital twins in 2018.
Even if the survey focused on significant markets with large players and ample initiatives in Industrial IoT, manufacturing and so forth that is pretty impressive.
When adding that according to that same March 2018 survey the number of participating organizations using digital twins is expected to triple by 2022, accelerating growth is indeed a term we can use.
The impact of more IoT digital twin initiatives on the market of manufacturing and Industry 4.0 IoT platforms
The impact of that rapid growth in digital twin initiatives (in the scope of IoT) obviously shows in the market of all sorts of vendors: the demand for digital twin support (along with augmented reality, edge capabilities and artificial intelligence), for example impacts the evolution of the IoT platform market, certainly that of Industrial IoT platforms with strong edge intelligence capabilities to give just one example of affected/involved solutions.
Most of the platforms in MachNation’s IoT Edge ScoreCard 2018, including FogHorn, Cumulocity IoT, Telit, Siemens (MindSphere), Litmus Automation, ClearBlade and so forth already have (or deployed initiatives to have) digital twin capabilities. Earlier 2018 Litmus Automation announced a partnership with ROHM for an enhanced smart factory IoT system with digital twins in the cloud, Cumulocity IoT (Software AG) has its digital twin and other connectivity-oriented services mentioned as examples of the deeper reach into Industrial IoT use cases by Forrester (Cumulocity IoT uses the Apama Streaming Analytics Platform of Software AG), the list goes on. Also Industry 4.0 platform relayr which we mentioned recently in the scope of a new investment round uses AI to offer applications for digital simulation of product behavior.
In the context of Hannover Messe 2018 it’s worth noting that many leading players in the digital twin market are from the US or Germany; two of the four countries covered by the Gartner digital twin announcement.
These leading digital twin players (and pioneers) include GE, IBM, PTC, Oracle, Microsoft and more from the US and Siemens, SAP, Bosch, Software AG and more from Germany. We should also mention others of course such as French Dassault Systèmes etc.; this list is not exhaustive.
As digital twin initiatives keep expanding across verticals (from automotive, manufacturing, transportation, healthcare, resources industries to smart cities and consumer-oriented applications) and across use cases (from machinery, equipment and other asset monitoring, product design and actual production, dynamic optimization to predictive maintenance), more vendors take initiatives.
End 2017, for instance, Industrial IoT fog computing specialist FogHorn Systems received a Series B round of funding and, on top of expanding its global footprint (FoghHorn is also at Hannover Messe 2018) the company wants to further invest in its analytics, machine learning and other advanced data and AI technologies, which among others enable the creation and modification of digital twins.
One of the reasons why we mention IoT platforms here is not just because of the role they play in digital twin initiatives but also because of the market evolutions that leave no doubt. And there is more than what we’ve mentioned so far.
Take the February 2018 Smart Manufacturing Platforms Assessment by ABI Research. As mentioned previously, Pierce Owen, Principal Analyst at ABI Research, stated that in order to remain relevant IoT platforms should work with suppliers of other transformative technologies to provide the most valuable functions and components, among others digital twin functionality.
And that’s what many are doing or have done. ABI Research also mentioned FogHorn Systems as a key innovator in real edge computing and complex event processing at the edge (and as said investing even more in digital twins with its several well-known industrial investors ).
The clear leader of smart manufacturing platforms for ABI, however, is Siemens’ Mindsphere that, given its focus and positioning is all the way into digital twin technology.
At a Siemens analyst event end 2017, the digital twin was all over the place and in a January 2018 market note from IDC (based upon that Munich Siemens Innovation Day 2017) simply called MindSphere and digital twins the key pillars of Siemens’ digital business strategy (which is in fact the title of the note).
And of course many of the leaders, including Siemens which will be extremely visible in the digital twin scope this year, at Hannover Messe 2018 where the digital twin, how else could it be, is even more present than in previous years (again, not just IoT platforms and manufacturing IoT platforms but also 3D digital tools, VR and AR, digital twin innovations from Fraunhofer, ample highly vertical solutions providers, mixed-reality software, user interfaces and a bunch of hardware).
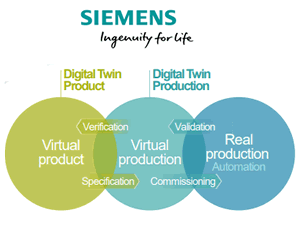
He continued: “Through the knowledge gained from MindSphere, we are also able to continuously optimize the entire value chain of our customers”.
Four Gartner digital twin best practices for CIOs
Back to the Gartner digital twin announcement in which the research firm as said also shares advice for CIOs in the form of digital twin best practices.
These four best practices aim to tackle the challenges in creating and maintaining digital twins, which is “not for the faint hearted” as Gartner research director Alexander Hoeppe, research director puts it.
The four Gartner digital twin best practices to structure and execute digital twin initiatives appropriately in order to tackle those key challenges in building and maintaining them in a bit more detail below the graphic.
Digital twin best practice 1: Involve the entire product value chain
Digital twins can help in tackling some essential supply chain challenges Gartner says.
Among these challenges faced by supply-chain officers: a lack of cross-functional collaboration or a lack of supply chain visibility. Therefore, investments in digital twin projects should be made value chain driven to enable product and asset stakeholders to govern and manage products, or assets like industrial machinery, facilities across their supply chain in much more structured and holistic ways.
When engaging the supply chain in digital twin initiatives, CIOs should incorporate access control based on the sensitivity of the content and the role of the supplier.
Digital twin best practice 2: Establish well-documented practices
Industry 4.0 projects require well-documented data models across each stage in the overall value chain, from design/prototyping to the consumer.
Documented practices in the construction/modification of digital twins are obviously key too and digital twins play across various parts of the overall value chain.
Standardization of modelling practices enables easier understanding, modification and collaboration and ensures long useful digital twin life cycles. Gartner: Best-in-class modelling practices increase transparency on often complex digital twin designs, and make it easier for multiple digital twin users to construct and modify digital twins collaboratively. Best-in-class modeling practices attempt to minimize the amount of effort to enable changes within the digital twin or between the digital twin and external, contextually important content
Digital twin best practice 3: Include data from multiple sources
Digital twins are hungry for data and if the digital twin architecture allows the access and use of data from multiple sources, additional data allow for operations, simulations and analysis beyond the geometric model.
It is difficult, Gartner emphasizes, to anticipate the nature of the simulation models, data types and data analysis of sensor data that might be necessary to support the design, introduction and service life of the digital twins’ physical counterparts.
Gartner: While 3D geometry is sufficient to communicate the digital twin visually and how parts fit together, the geometric model may not be able to perform simulations of the behavior of the physical counterpart in use or operation and the geometric model may not be able to analyze data if not enriched with additional information.
Digital twin best practice 4: Ensure long access life cycles by avoiding proprietary software
While long useful digital twin life cycles are served by well-documented and standardized modelling practices, proprietary implementations and vendor lock-in are a risk for digital twins with a long life cycle (e.g. buildings, aircraft, ships, factories, machinery,…).
The life cycles of such digital twins extend beyond the life spans of the formats for proprietary design software that probably were used to make them and data storage means, says Gartner: digital twins created in proprietary design software formats have a high risk of being unreadable throughout their service life, CIOs can guard against this by setting a goal for IT architects and digital twin owners to plan for the long-term evolution of data formats and data storage.
More about the Gartner digital twin best practices in the press release where you can also find the earlier mentioned data. Gartner defines a digital twin as a virtual counterpart of a real object, meaning it can be a product, structure, facility or system.
Gartner clients can find a detailed explanation and more advice and findings in the Gartner report, “Four Best Practices to Avoid Digital Twin Failures.”
Top image: Shutterstock – Copyright: Zapp2Photo – Icon set: Shutterstock – Copyright: monicaodo – All other images as well as logos, names and brands are the property of their respective mentioned owners.