Dundee Precious Metals (DPM) is headquartered in Toronto (Canada) and explores, among others, an underground copper and gold mine in Bulgaria. Other countries include Namibia and Armenia.
Several years ago the business wanted the IT division to look at various new possibilities to enhance pro-activity, safety and operational longevity, to better understand what was happening in the mine and to see what could be done with all the assets, processes, acquired insights etc. to, in the end, increase productivity, a primary goal in Industry 4.0.
We need disruptive innovation in the mining sector, as well (Rick Howes, CEO Dundee Precious Metals)
It became an Industrial Internet of Things and Industry 4.0 project with multiple benefits, process optimizations, productivity improvements and technological aspects, also making Dundee Precious Metals one of the pioneers in the mining and metals industry to tap into the possibilities of the Industrial Internet and actionable data from connected assets.
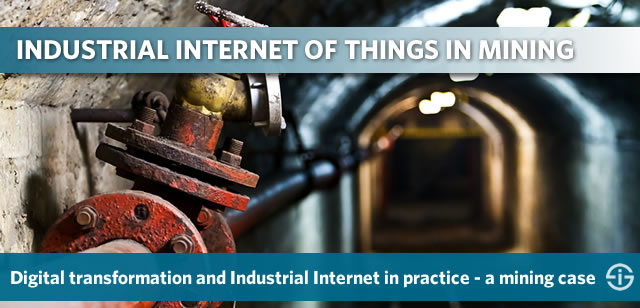
Digital transformation, the Internet of Everything and disruptive innovation in the mining industry
The mining industry has several challenges. Depending on the types of mined materials (‘commodities’), these range from lowering/fluctuating commodity prices and demand to labor shortage, a changing competitive landscape, safety issues and productivity optimization.
While you might not associate mines with digital transformation and disruption, several mining companies (Glencore, Rio Tinto and more) have been early in leveraging the Internet of Things.
Still, there is a lot of work ahead. According to IDC, 77 percent of mining companies across the globe are just embarking on their digital transformation journey. And in that journey data (analytics) and the Industrial Internet of Things are of course two major enablers.
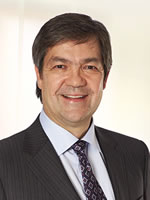
Dundee Precious Metals is clearly not at the beginning of that journey. Early 2016, CEO Rick Howes, wrote an article, entitled ‘We need disruptive innovation in the mining sector, as well‘, among others elaborating on the challenges and the transformation of mining companies into knowledge-based companies.
As an asset-intensive industry that operates in sometimes harsh conditions this seems at the same time very possible, yet – to say the least – not the easiest task ever.
Still, as IDC wrote in 2015, “the future of mining is to create the capability to manage the mine as a system – through an integrated web of technologies such as virtualization, robotics, Internet of Things (IoT), sensors, connectivity and mobility – to command, control and respond”.
Turning a mining operation into a knowledge-based ecosystem of people, processes, assets, data and optimization
How do you achieve all that – and more – in an underground mine and what about mines in very remote locations?
Moreover, there is a lot that can be connected for the sake of increased productivity, higher worker safety and satisfaction and the evolution to the knowledge-based state as Rick Howes describes it in the mentioned ‘disruptive innovation’ article.
Time to take a look at what Dundee Precious Metals did with the Internet of Things and connected technologies and what outcomes it achieved.
We mentioned the intentional tasks above. The businesses really wanted IT to, as they called it, take the lid off the mine: taking ‘old processes’, including paper reporting and reactive maintenance to a new way where information would be available in real-time, maintenance became pro-active and so forth.
Dundee Precious Metals also wanted to increase the production at its Bulgarian mine by 30 percent. Productivity increases in a mining operation obviously consists of several factors.
In a video on YouTube, Mark Gelsomini, Corporate Director of IT, explains how the IT crew wanted to see all the possibilities to enhance that productivity, without additional workers or vehicles, by taking that lid of the mine and really dive deep into various parameters which give an overview of how the mining operations happened today.
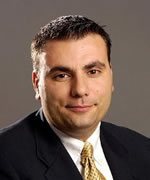
These parameters included, among others the location of miners and of mining equipment, actual ‘production’ (read: the number of filled buckets) and the state of the vehicles (and there are quite some of those in mines).
While it’s easy to see why location (and thus also movement) and filled buckets are related with productivity, maybe it’s less obvious with vehicles. But you know what happens when a vehicle or whatever kind of assets in your production and supply chains fail: interruptions, impacting productivity. That’s why vehicle status monitoring, among others for predictive maintenance, is important and why it matters to track various parameters of the vehicle’s conditions.
The connectivity and communications challenge in mining in practice
In order to keep track of all these parameters and turn the data into actionable intelligence to achieve that productivity gain and all the other (intermediate) goals, you obviously need a communications system to, well, communicate, and to transmit the data of sensors and connected assets/devices.
In an underground mine traditionally Wi-Fi didn’t turn out to be the best solution, except if workers are in the same tunnel as is explained in the case study PDF (see below). If you don’t have Wi-Fi or any other form of connectivity you need to wait until you get production data in paper as mentioned earlier and you don’t have insights in whatever interruptions happen right now and right here, real-time
This is where, among others, Cisco technology came in (more partners in the overall projects below) and a wireless IP network was realized. Connectivity obviously means transmission of data from ‘things’ and, in this case also the connection of IP phones, in-vehicle tablets, surveillance cameras, PLCs on the conveyor system in the mills, lights and so forth.
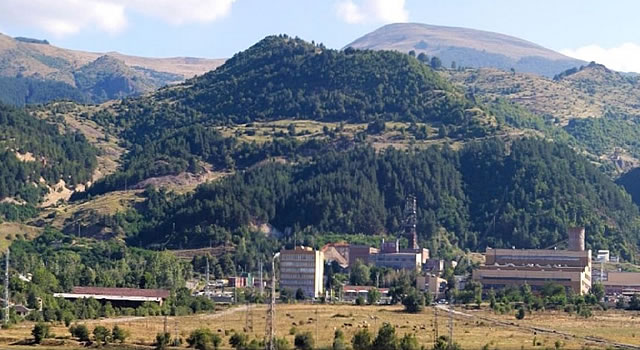
Drivers have an overview of the production and can use their tablets in case of an issue that impacts productivity to share video of the issue with an expert.
Last but not least, RFID tags are added to the caps of miners and to vehicles. The signals are leveraged in a custom application, which adds to the safety of miners.
Achieved benefits in the Dundee Precious Metals IoE project
In 2014, four years after the productivity increase goal was set, Dundee Precious Metals had achieved a 400 percent production increase instead of the 30 percent it wanted to realize.
On top of the productivity increase, other benefits were realized (you can read more about them all and about the technology stack) in the sources we consulted.
RFID tags are added to the caps of miners and to vehicles
Among those realized benefits are:
- Enhanced collaboration and ability of real-time communication.
- Remote problem solving and pro-active maintenance.
- Improved safety.
- Enhanced asset utilization (e.g. vehicles).
- Lower communication costs.
- A better way of planning work and production.
- Bye bye slow paper-based reporting, hello real-time data.
The solution was also applied in other mines and additional benefits were explored, among others for open-pit environments and health monitoring.
Check out the mentioned video in which Mark Gelsomini, Corporate Director of IT at Dundee Precious Metals, tackles the case.
Consulted and additional resources on the Dundee Precious Metals Industrial Internet case:
- The 2014 case study by Cisco with all the practical technological aspects (PDF opens).
- A case study summary.
Top image: Shutterstock – Copyright: raifu – All other images are the property of their respective mentioned owners. Disclaimer: we have no relationships with any of the mentioned companies. The top image does not show the mine of Chelopech.