The manufacturing industry is at the center of the Industry 4.0 movement, which has gradually expanded into other industries. Manufacturing is also the largest industry from an IoT spending perspective.
That’s not really a surprise as IoT and cyber-physical systems are key in Industry 4.0. There are ample of use cases for IoT in the manufacturing space and obviously various projects have been realized to enhance customer service, improve operations/efficiency and develop new services and revenue sources thanks to digital transformation initiatives and the usage of IoT in manufacturing, leveraging Industrial IoT (IIoT).
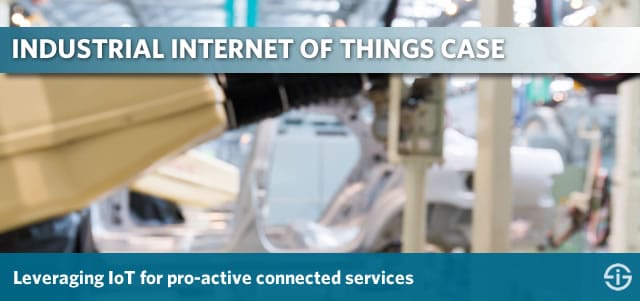
The Internet of Things to build connected services and increase uptime of robots
The approach which automation multinational and Industry 4.0 pioneer ABB took in the area of industrial robotics is a good example of how these benefits can be achieved. In our series of IoT examples we take a look at the initiative and its results.
As is often the case, ABB was driven by challenges and opportunities that are also valid in many other industries. So, regardless of your industry: the case might be useful for you too. Note: we have no relationships with any of the mentioned companies and our aim is to inform and inspire.
The power of the Internet of Things comes from the ability to collect a lot of data and convert that into useful information (Bertil Thorvaldson, Product Manager, ABB Robotics)
ABB (short for Asea Brown Boveri) is a Swedish-Swiss multinational which is, among others, active in energy and automation. One of the main activities of the company is the production of industrial robots, cobots, and manufacturing services for a variety of industries, ranging from automotive to electronics and, increasingly, the food industry.
Such industrial robots are indeed not the kind of robots you would see at the Consumer Electronics Show but robotics systems as they are mainly used for manufacturing. On top of making and selling such industrial robots, ABB provides a series of services. You can imagine that this kind of equipment doesn’t get unpacked and plugged in just like that.
Moving from reactive services to pro-active services and real-time monitoring
Even if the industrial robotics industry and the manufacturing environments where they are used are already very information-intensive, highly automated and technology-rich, they also have digital transformation opportunities.
In the case of ABB this was mainly in building a connected industrial robotics environment and offering with connected services. In the past, ABB only could offer maintenance and support services to its customers when they had an issue with an industrial robot after the facts.
It’s no longer good enough to have a fast response time, you need to act before something goes wrong (Rene Nispeling, Product Manager for Customer Service, ABB Robotics)
Since smart manufacturing and industrial robots are about optimizing efficiency, minimizing downtime and continuously operating at optimal performance, both regards quantity and quality, a clear and present challenge existed: how can we make sure that our customers are served far faster?
In many industries there obviously are agreements on service, reserve machines and more but nothing beats pro-activeness, especially as it opens doors to new services, for instance regarding real-time performance insights.
Thanks to its Internet of Things initiative the company now can avoid the interruption of operations in case of issues with its products. You can imagine what it means from a customer perspective if a robot keeps functioning instead of it being out for one or a few days in manufacturing environments.
Data at the service of the customer, business continuity, efficiency and new offerings
Obviously, data is at the center of this project as it offers plenty of useful information regarding, among others diagnostics and so forth.
With the Internet of Things it’s possible to get real-time actionable information that can form the basis for new services (Bertil Thorvaldson, Product Manager, ABB Robotics)
From a technological perspective the whole initiative was done by using an API of the Jasper Control Center (IoT platform) in connection with the service business system.
To summarize some of the business benefits:
- The ability to move from reactive support to proactive maintenance and real-time identification of issues without the need to send an engineer to detect the cause of the issue (in most cases).
- The ability to offer this kind of support 24/24, 7/7, which in a manufacturing environment is a clear gain as well.
- Reduced down-time and thus higher efficiency and productivity with a possibility to in some cases solve issues from a distance (which is important as the robots of ABB are a bit all around the globe and not always in the easiest to reach locations).
- Increased customer service and enhanced customer experience thanks to the mentioned benefits and for all the clear reasons in industries where uptime is critical.
- The ability to develop a new service, which was launched in the Summer of 2016 by ABB Robotics and is called ‘Connected Services’, being part of what ABB calls the Internet of Things, Services and People (IoTSP) and is available via the company’s Robot Care Service Agreements. Note: the IoTSP vision of ABB stretches beyond the robotics activities.
- The new services, possible with this Internet of Things, Services and People approach include services regarding condition monitoring and diagnostics, backup management, remote access, asset optimization and fleet assessment, delivered via a web application, called MyRobot, as the infographic illustrates.
Sources and case description
Actionable data/intelligence, leading to higher productivity and new services, thanks to IoT.
- Various platforms and technologies: as mentioned, the Jasper platform (an IoT connectivity management platform), 3G connectivity and for field services Salesforce Field Service Lightning, Analytics Cloud and IoT Cloud.
- Type of use case: manufacturing operations, field service, manufacturing equipment maintenance, predictive maintenance, connected industry.
- More about the services on this page of the ABB site.
- More about the various components of that IoTSP approach and the mentioned connected services in the infographic below (full PDF version here).
- A written case study by the Jasper people in this PDF.

Top image: Shutterstock – Copyright: Nonchanon – All other images are the property of their respective mentioned owners.