TQM stands for Total Quality Management. It is an approach to management that focuses on continuously improving organizational processes, products, and services. TQM aims to meet or exceed customer expectations and customer experience by involving all employees in the quality improvement approach.
TQM strives to achieve optimal customer satisfaction by ensuring that every aspect of an organization’s operations is geared toward delivering high-quality products or services. This includes everything from product design and development to production, distribution, and customer service.
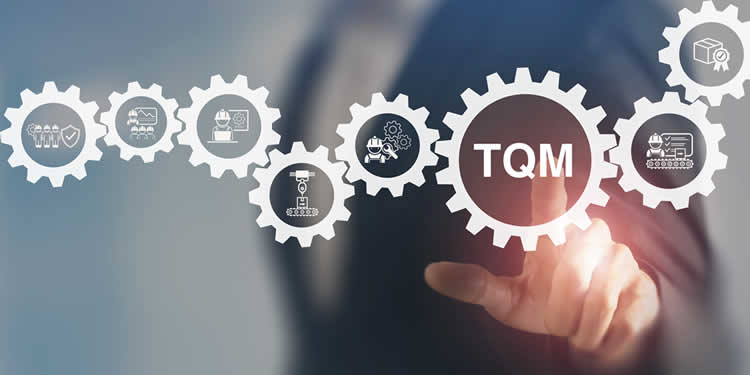
TQM is a holistic approach involving all organizational levels, from senior management to frontline workers. It involves using data and statistical analysis to identify and measure quality problems and monitor progress toward continuous improvement (also sometimes called ‘Kaizen’) goals. Organizations can improve quality, reduce costs, increase efficiency, and enhance customer satisfaction through this approach. It’s clear that TQM is oriented on long-term success, not quick fixes or the short term. A look at the meaning of TQM today and how it relates to IT and digital transformation with Industry 4.0 and the related notion of Quality 4.0.
The critical role of IT in TQM
Information technology (IT) obviously has become vital for TQM as it provides tools and technologies that enable organizations to manage and improve the quality of their products and services. Moreover, digital technologies and the whole datasphere nowadays play a crucial role in virtually all organizational operations and the activities of employees on all levels. Here are some of the functions that IT plays in TQM:
- Data collection and analysis: IT can provide systems for collecting and analyzing data related to quality metrics, such as defect rates, customer complaints, and process performance. This data can be used to identify areas for improvement and track progress toward quality goals.
- Quality management systems: IT can provide software for managing quality processes, such as document control, corrective and preventive action, and audit management. These systems can help ensure that quality procedures are standardized and consistently applied across the organization.
- Automation of quality processes: IT can automate quality processes, such as inspection and testing, to reduce errors and improve efficiency. This can help ensure that products and services meet or exceed customer expectations.
- Communication and collaboration: IT can facilitate communication and cooperation between departments and teams involved in quality management. This can help ensure that everyone is working towards the same quality goals and that information is shared effectively.
- Customer feedback: IT can provide systems for collecting and analyzing customer feedback, such as surveys, social media monitoring, and customer metrics on levels such as customer satisfaction and customer-centricity. This can help organizations understand customer needs and preferences and identify opportunities for improvement.
In summary, IT can help organizations implement TQM by providing tools and technologies that support data analysis, quality management, automation, communication, collaboration, and customer feedback.
Where TQM comes from – a brief overview with principles and methods
TQM has its roots in the quality management practices that emerged in Japan in the 1950s and 1960s. At that time, Japanese companies competed in a global market that American and European firms dominated. To stay competitive, Japanese companies began to focus on improving the quality of their products and services.
A key role in the development of TQM was played by Dr. W. Edwards Deming, an American statistician who went to post-war Japan in the 1950s to teach quality management principles with a US government mandate. Deming’s ideas, which emphasized the importance of statistical analysis and continuous improvement and built upon the work and ideas of Walter A. Shewhart (the father of statistical quality control and the control circle/cycle or Shewhart cycle), significantly impacted the Japanese industry and became known as the “Deming Method.”
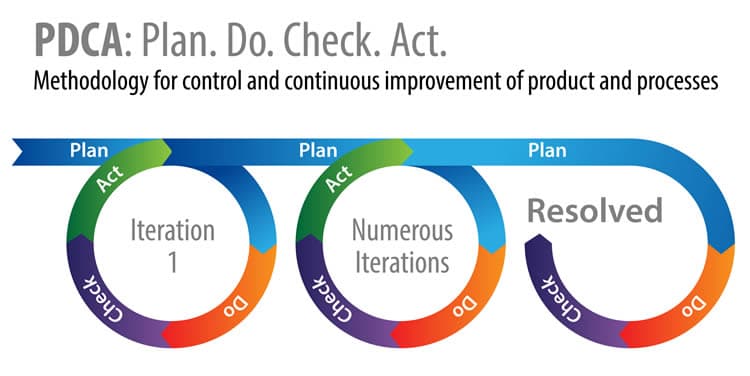
This Deming method, also known as the Deming cycle or PDCA cycle, consists of four steps, which form the acronym PDCA:
- Plan: In this step, the organization identifies a problem or opportunity for improvement, sets objectives, and develops a plan to achieve those objectives.
- Do: In this step, the plan is implemented, and data is collected to measure the effectiveness of the plan.
- Check: In this step, the data collected in the previous step is analyzed to determine if the plan effectively achieved the objectives.
- Act: In this step, the organization takes action based on data analysis. If the plan was effective, it is standardized and integrated into the organization’s processes. If the plan is ineffective, the organization revises the plan and repeats the PDCA cycle.
The Deming method emphasizes the importance of continuous improvement and the use of data to drive decision-making. It is widely used in quality management and process improvement initiatives. It also is important in lean manufacturing and Six Sigma, two quality control concepts that came after TQM and became more popular but have a lot in common with it. Deming also was a strong believer in the role that all employees, more ‘ordinary workers’ included, played in quality control.
Another important figure in the development of TQM was Joseph Juran, an American engineer. Juran emphasized the importance of customer satisfaction and introduced the concept of “fitness for use,” which became a central idea in TQM.
According to Juran, “fitness for use” refers to the ability of a product or service to meet the needs of its users or customers. Juran believed that quality should be defined in terms of customer needs and expectations and that a product or service should be designed and produced with those needs and expectations in mind. This requires a deep understanding of customer requirements and a commitment to meeting those requirements through continuous improvement.
To achieve fitness for use, Juran proposed a three-step process:
- Identify customer needs and expectations: This involves understanding the needs and expectations of customers through market research, surveys, and other feedback mechanisms.
- Translate customer needs into product or service requirements: This involves translating customer needs and expectations into specific, measurable requirements that can be used to design and produce the product or service.
- Develop and produce the product or service: This involves designing and producing the product or service to meet the identified requirements and continuously monitoring and improving the process to ensure that the product or service remains fit for use over time.
Juran believed that achieving fitness for use requires a commitment to quality at all levels of the organization, from top management down to the individual worker. It requires a focus on understanding customer needs and expectations and a commitment to meeting those needs through continuous improvement and innovation.
In the 1980s, TQM gained popularity in the United States, where companies faced increasing competition from Japan and other countries. TQM became a popular approach to quality management, and many companies adopted TQM principles and practices to improve their products and services.
Today, TQM continues to be an essential approach to quality management in many organizations worldwide. It has evolved to include new tools and techniques, but the core principles of TQM remain focused on continuous improvement and customer satisfaction.
What is the link between TQM and Industry 4.0?
TQM and Industry 4.0 are closely linked, as both approaches focus on improving quality and efficiency through technology and data.
Industry 4.0 refers to the automation and data exchange trend in manufacturing technologies focusing on digitization and digital transformation, whereby ecosystems play an important role. It leverages various technologies such as Industrial IoT, big data and analytics, AI and machine learning, robotics, cloud computing etc. to create “smart factories” and build digital supply chains that are more efficient, flexible, and responsive to customer and partner needs.
TQM and Industry 4.0 share several common goals, such as improving quality, reducing waste, and enhancing customer satisfaction. However, Industry 4.0 provides new opportunities for TQM by enabling the collection and analysis of real-time data from manufacturing processes, which can be used to identify quality issues and optimize production.
For example, in an Industry 4.0-enabled factory, smart sensors can collect data on production processes, such as temperature, pressure, and vibration. This data can be analyzed in real-time to identify quality issues and optimize the production process. This enables organizations to detect quality problems before they become more severe and costly to fix.
Moreover, Industry 4.0 can also help organizations to enhance customer satisfaction by enabling more customized products and services. For example, with advanced technologies, manufacturers can offer products tailored to individual customer needs, improving customer satisfaction and loyalty.
In summary, TQM and Industry 4.0 are closely linked, as both approaches aim to improve quality and efficiency through technology and data. By leveraging the opportunities provided by Industry 4.0, organizations can enhance their TQM practices and achieve better outcomes for their customers and stakeholders.
Quality 4.0: integrating digital technologies and quality management systems
Regarding quality management and Industry 4.0, we often see the term Quality 4.0 (just as some people talk about Logistics 4.0, etc.). So, Quality 4.0 is a term used to describe the integration of digital technologies and quality management systems.
It is a concept based on the principles of Industry 4.0 and uses the aforementioned digital technologies (artificial intelligence, the Internet of Things, big data analytics, cloud and other related technologies such as digital twins) to enhance quality management processes.
Quality 4.0 aims to improve quality management systems by enabling real-time monitoring, predictive maintenance, and data-driven decision-making. It also aims to increase efficiency and reduce costs by automating quality control processes and facilitating continuous improvement through data analysis.
In essence, Quality 4.0 represents a shift from reactive quality control to proactive quality assurance, where quality management systems are integrated with digital technologies to enable a more agile, efficient, and effective quality management process.
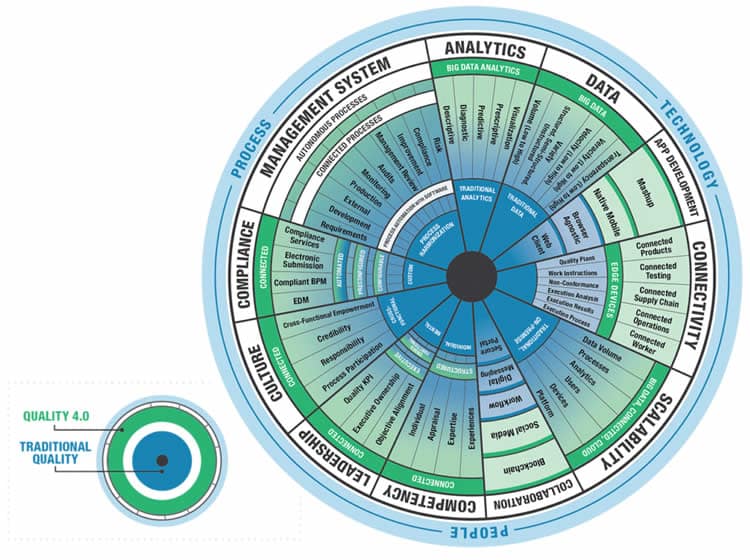
The principles of TQM in a nutshell
The principles of Total Quality Management (TQM) are:
- Customer focus: The primary focus of TQM is to meet or exceed customer expectations. Organizations must understand the needs and expectations of their customers and strive to deliver high-quality products and services that meet those needs.
- Continuous improvement (Kaizen): TQM is an ongoing improvement process. Organizations must continually strive to improve their products, services, and processes to meet changing customer needs and expectations.
- Employee involvement: Total Quality Management means that ALL employees are involved in the quality improvement process. Staff at all levels of the organization should be involved in identifying quality problems, developing solutions, and implementing improvements.
- Process orientation: TQM focuses on improving the quality of organizational processes. Organizations can reduce defects, waste, and costs by improving efficiency and effectiveness.
- Data-driven decision making: TQM relies on data and statistical analysis to identify quality problems and measure progress towards improvement goals. Organizations must collect, analyze, and use data to make informed decisions about quality improvements.
- Leadership involvement: TQM requires leadership commitment and involvement. Senior management must provide the necessary resources and support for quality improvement initiatives and be actively involved in driving the TQM process.
- Supplier partnerships: TQM involves developing partnerships with suppliers to ensure they provide high-quality inputs that meet the organization’s needs. Organizations must work with suppliers and ecosystems to improve their quality and reliability.
- Strategic planning: TQM requires strategic planning to ensure that quality improvement initiatives are aligned with the organization’s overall goals and objectives.