The next challenge for Industry 4.0 is scaling up. Yet, many organizations struggle to scale, with the convergence of IT and OT (operational technology) and skills/capabilities/talent being two major challenges to realize smart factories. An overview.
Organizations expect greater benefits from their smart factory initiatives in the future, as programs become more stable as “teething” issues are resolved
By 2023, the manufacturing industry could add $2.2 trillion of value to the global economy due to productivity gains achieved through smart factory initiatives. Yet, even if the expected average added value from smart factories is also high with $1.9 trillion and expectations regarding smart factory benefits are on the rise, several actions need to be taken before that value is realized – with an emphasis on scale.
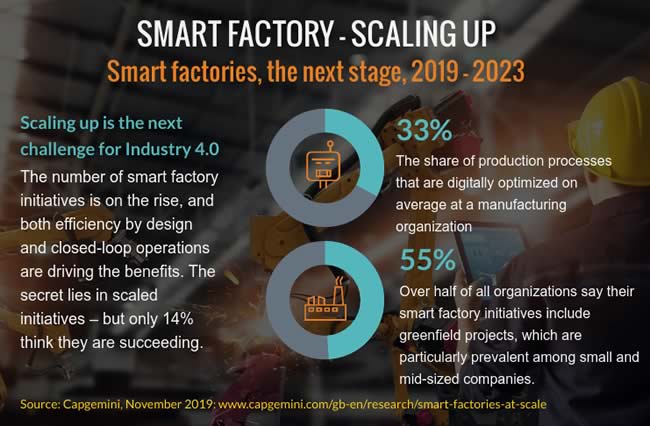
Only fourteen percent of organizations consider their smart factory deployment so far a success, and scaling proves to be hard. In fact, over 50 percent find the deployment and integration of digital platforms and technologies a significant challenge to scale up their smart factory initiatives.
Data readiness and cybersecurity are the second major challenge faced by manufacturers in achieving smart factory performance at scale
Still, with the expected benefits, the fact that there are more smart factory initiatives – and thus also examples – and several (other) market dynamics, manufacturers intend to invest more than ever in smart factory projects. The two main challenges to scale up, which is the next challenge in Industry 4.0, are 1) IT and OT convergence, and 2) the set of capabilities and skills that are required to drive digital transformation in smart manufacturing, including cross-functional capabilities, digital talent, and soft skills.
These are some findings from a November 2019 report from the Capgemini Research Institute. According to the report, an increase of the right smart factory investments and the tackling of challenges such as the mentioned ones could make smart factories add at least $1.4 trillion to the global economy by 2023.
So, what needs to happen before this is possible, and how can this value be realized since, per the report, around two-thirds of it must still be accomplished? Let’s start with the beginning: the smart factory and some takeaways on the digital transformation of manufacturing from the report.
Smart factories – connectivity, automation, data
In order to know what we talk about, a few words on the smart factory since it’s not really a formally defined term although we all more or less know what it means.
Efficiency by design and closed-loop operations drive smart factory benefits equally
The smart factory, a typical term from the Industry 4.0 and smart manufacturing jargon, is often linked to its enabling technologies, essentially revolving around Industrial IoT, big data analytics, production techniques, connected physical equipment and what can be done with it in a cyber-physical scope: the Internet of Things and sensors, the mentioned convergence of IT and OT, new means of manufacturing, (cloud-based) platforms, enabling technologies (AI, ML,…) interoperable and highly connected systems/platforms and the analysis and usage of data from ample sources including machines, turned into actions and decisions (automation and semi-automated), play an essential role in it.
As the graphic from the report’s infographic below shows, cybersecurity and data readiness rank second as the most often cited challenge to scale digital factory projects.
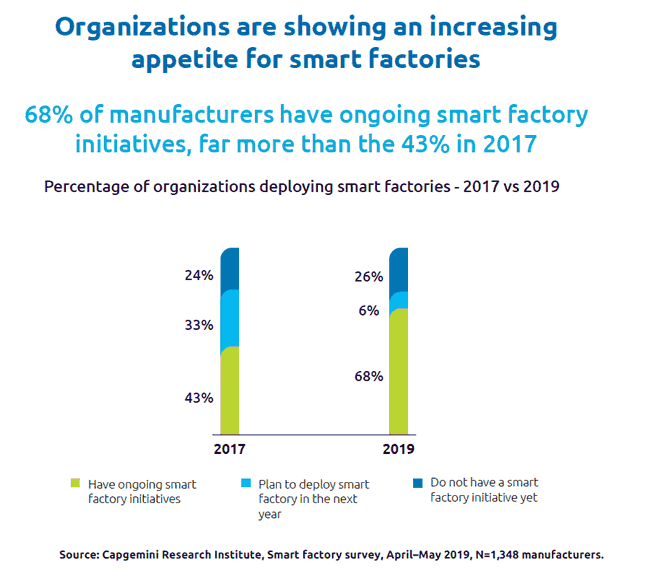
The ‘smart’ aspect is also related to the smart and agile automated system a smart factory is often believed to be, with capacities to adapt based upon real-time data, making the manufacturing process more or less autonomous although that is more a vision and de facto manual and semi-autonomous decisions and optimization will remain essential for many and many years to come. Ask all those factories that started projects and had to end them because machines weren’t capable (yet?) of delivering the same quality as people with notable examples in the aviation industry.
PLM, MES/SCADA and robotics are key components of industrial architecture. However, the main areas of investment for at-scale deployments are IoT and AI
The smart factory is about more than the technologies and data from the edge. It also includes the aspects of people, culture, collaboration supply chains, and most of all, goals, use cases and capabilities offered by all this increasingly available data. After all, a factory without smart – measurable – goals enabled by knowledge from data can hardly be called smart, can it? Such purposes generate a large chunk of that $1.4 trillion with, for instance, enhanced productivity and reduced downtime.
In the announcement of its report, entitled ‘Smart Factories @ Scale‘ (PDF downloads), Capgemini defines a smart factory as follows: “A Smart Factory leverages digital platforms and technologies to gain significant improvements in productivity, quality, flexibility, and service.”
Schneider Electric, mentioned in the announcement of the report with a quote from Mourad Tamoud who is, EVP, Global Supply Chain Operations at the company, defines a smart factory as follows: “Leaping forward from traditional machine automation, the Smart factory deploys smart manufacturing technologies for Industry 4.0. Physical machines are fitted with smart sensors and are connected to a cloud network where it uses data from connected operations and production systems to learn and adapt to spontaneous situations and make real-time decisions”.
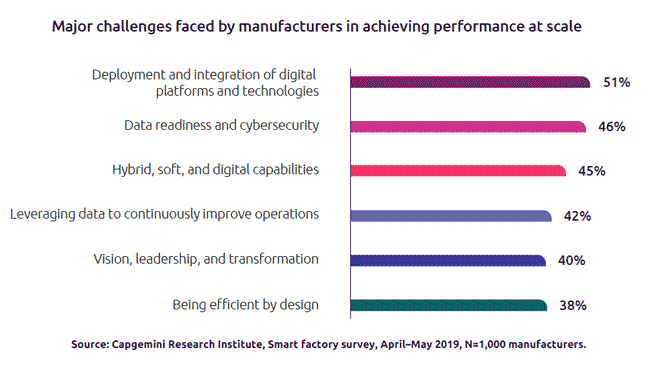
Of course, there are more smart factory definitions out there. Most of them point to the digitized and connected aspect of the factory and the smart factory as an evolving given in smart manufacturing and Industry 4.0, along with a list of additional capabilities and technologies including the ones mentioned and other usual suspects such as artificial intelligence and machine learning (a bit everywhere throughout the systems and the data and automation/decision and predictive aspects), big data analytics, advanced robotics, digital twins and simulation, additive manufacturing, etc.
On the capacity side agility, connectedness, continuous optimization and proactive capabilities are some of the main ones.
For Capgemini, the three key technologies that enable the smart factory are 1) connectivity (leveraging IIoT to collect data), 2) intelligent automation (a category including many things such as advanced robotics and drones but also MES and SCADA), and 3) cloud-scale data management and analytics.
Investments in smart factories: outlook 2023
Time for some key takeaways from the “Smart Factories @ Scale” report. No matter how you turn it, the data and what it enables, especially when leveraged for integrated purposes, is essential in the smart factory.
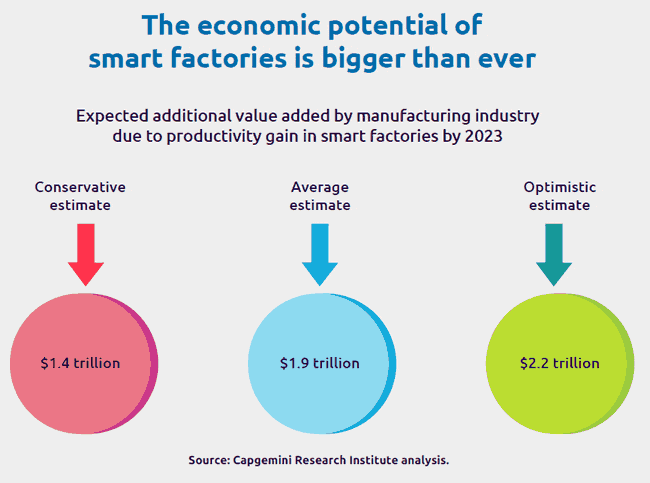
As Jean-Pierre Petit, Director of Digital Manufacturing at Capgemini, puts it: “To unlock the promise of the smart factory, organizations need to design and implement a strong governance program and develop a culture of data-driven operations.” How true.
Findings on the smart factory plans of organizations – and their impact
- In comparison with a similar report from two years ago, the smart factory appetite of organizations is more significant than ever, even if few consider smart factory deployments so far a success.
- According to Capgemini, there’s an increasing appetite and aptitude for smart factories, and organizations are moving on their journey of transformation, with one-third of factories already being transformed into smart facilities.
- In the next five years manufacturers plan to create 40 percent more smart factories – and that goes hand in hand with an increase of annual investments by 1.7X compared to the last three years.
- Also over the next five years, smart factories could increase the value they add to the global economy up to even $2.2 trillion. As the graphic shows, Capgemini’s conservative estimate is a value of $1.4 trillion and its optimistic forecast $2.2 trillion (the average expected additional value added by the manufacturing industry due to smart factory productivity gains by 2023 being $1.9 trillion).
- The percentage of organizations with ongoing smart factory projects has significantly increased over the past two years: while the 2017 report found that 43 percent of respondents had such projects, in the 2019 edition it turned out that 68 percent of organizations had ongoing projects.
Smart factory transformation – a roadmap and the importance of learning from performers and lighthouses
Capgemini also looks at how organizations can accelerate and secure their smart factory transformation and offers a smart factory roadmap, which it further details in the full report. Along with those reasons that make scaling harder and obviously overlap, they can provide additional guidance to organizations planning to do more.
Pointing back to the fact that there are more smart factories now, one has the opportunity to see how others are doing, especially with those famous lighthouses: an initiative launched a few years ago by the World Economic Forum whereby lighthouse manufacturing companies and lighthouse factories were listed, serving as beacons for others.
The list grew over the years. It’s not a surprise that Capgemini quotes Schneider Electric’s EVP, Global Supply Chain Operations, Mourad Tamoud, since the company had its factory in Le Vaudreuil, France, on the first list of lighthouse factories and, since 2019, its Indonesian factory in Batam is also on the list.
Per the report, learning from high performers (10 percent of the sample of respondents; the report is based on a survey of 1,000 executives from companies with a smart factory initiative underway and 20 in-depth discussions with execs involved in a smart factory or project), is indeed advised.
These high performers (note: not the same as the lighthouses which aren’t mentioned by Capgemini) invest a lot in the foundations of smart factories. And these foundations, of course, are looked at in the report since they come back in the dimensions of smart factory transformation per Capgemini as the illustration from the infographic, below, shows (and they were also ranked in the challenges to scaling):
- Digital platforms, in particular, the deployment and integration of digital platforms and technologies, related to the IT and OT convergence part.
- Data readiness and cybersecurity, also mentioned in an IT and OT integration context – and a big challenge.
- Talent, in particular, digital talent, expanded with the other mentioned skills and capabilities, the whole lot categorized as soft, digital and hybrid capabilities.
- A well-balanced ‘efficiency by design’ and ‘effectiveness in operations’ approach (operational excellence).
- Leadership and vision.
- Governance and leveraging the power of data and collaboration (not separate but ‘part of’).
The graphic clearly shows how front-runners do better on all the mentioned fronts than experimenters and novices.
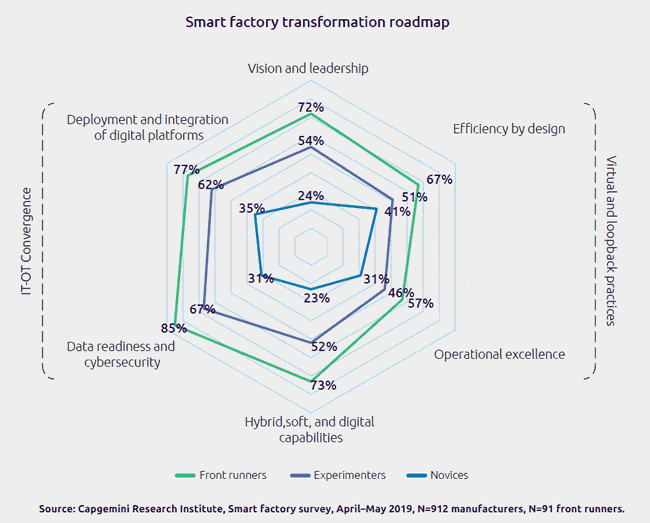
On top of looking at specific smart factories and smart factory projects it’s clear that in most countries across the globe there are now local and/or regional initiatives whereby manufacturers, policy-makers and other stakeholders come together to learn and change expertise, not to mention commercial initiatives and the ecosystems of some vendors, just for the sake of being complete since you know that of course.
More findings and final recommendations for smart factories
Download the full report (PDF opens) for more details with regards to various countries, insights into which manufacturing segments have done most on a smart factory level (and which segments will drive investments and efforts in the next years), analysis of the digitization and digitalization projects done and planned by manufacturers, additional challenges, key priorities and more.
By 2023, the manufacturing industry could add $2.2 trillion of value to the global economy due to productivity gains achieved with smart factory initiatives
Below are some additional takeaways Capgemini emphasized at the occasion of the launch of the report:
- 5G is poised to be a vital enabler of the smart factory for various reasons, including the fact that its capabilities would provide manufacturers the opportunity to introduce or enhance a variety of real-time and highly reliable applications per Capgemini.
- On a skills level, cross-functional profiles, such as engineering-manufacturing, manufacturing-maintenance, and safety-security will be essential to succeed, as are those soft skills, such as problem solving and collaborative skills.
- PLM, MES (manufacturing execution systems)/SCADA and robotics are key components of industrial architecture, but the main areas of investment for at-scale smart factory deployments are the Internet of Things (IoT) and artificial intelligence, which support data-driven operations, as well as remote and mobile capabilities.
- Productivity gains, improvements in quality and market share, and customer services are key components in the value that can be driven by smart factories. Efficiency by design and operational excellence through closed-loop operations make equal contributions. Closed-loop operations involve the use data generated by operations to optimize them in real time.
And to end, below is a last part of the infographic, summarizing the view per the survey/interviews on how organizations can accelerate and secure their smart factory transformation, building upon the foundations and challenges in scaling.
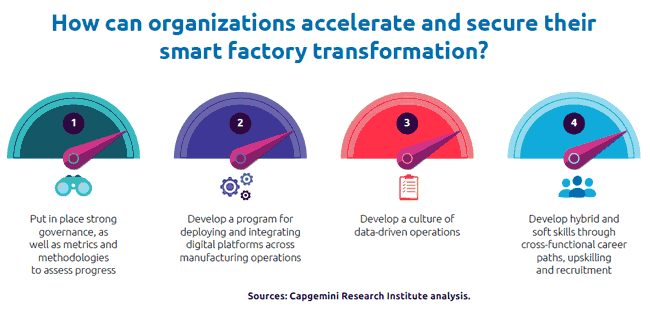
- Put in place strong governance, as well as metrics and methodologies to assess progress (smart factories, as said, are also about smart goals too; and smart also stands for Specific, Measurable, Achievable, Realistic, and Timely).
- Develop a program for deploying and integrating digital platforms across manufacturing operations.
- Develop a culture of data-driven operations. The essence of so many smart factory use cases, platforms and projects and of smart factories and, in the end, of the data-intensive end-to-end integration models of Industry 4.0.
- Develop hybrid and soft skills through cross-functional career paths, upskiling and recruitment.