What is operational technology (OT) and how is it different from IT and at the same time converging with information technology?
It’s impossible to talk about the evolutions in manufacturing, industrial transformation and Industry 4.0, innovations in areas such as Industrial IoT without mentioning the convergence of IT and OT.
While everyone has a good grasp of what IT is, for people who don’t have an OT background might wonder what OT or operational technology really means. Operational technology or OT is a category of computing and communication systems to manage, monitor and control industrial operations with a focus on the physical devices and processes they use.
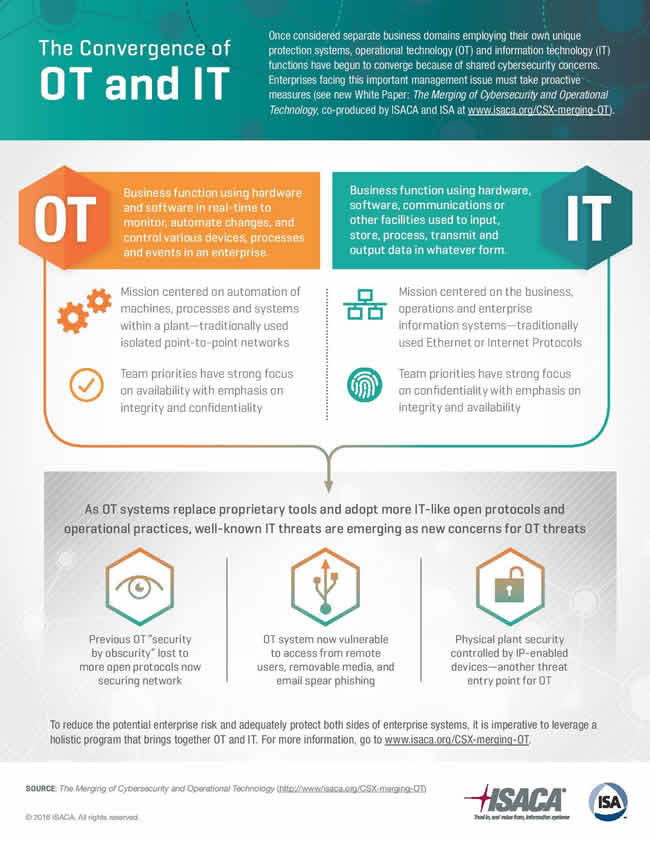
Operational technology, monitors and manages industrial process assets and manufacturing/industrial equipment. OT exists much longer than IT or information technology, more specifically since we started to use machinery and equipment powered by electricity in factories, buildings, transportation systems, the utility industry, etc. The term, however, is more recent. Essentially, OT is the hardware and software that keeps things, for instance factories, power plants, facility equipment etc. running.
Operational technology – definition, origins and evolution
While operational technology is about control and safety systems and industrial process assets, IT or information technology is about business and enterprise systems that store, process and deliver information.
The most often used definition of operational technology comes from Gartner: “Hardware and software that detects or causes a change through the direct monitoring and/or control of physical devices, processes and events in the enterprise”.
The definition from Gartner is more for IT people and that’s probably why it’s so popular. There are several other definitions of OT whereby some limit themselves to the lowest levels of the traditional automation pyramid (field level, control level, production level,…) while others go higher.
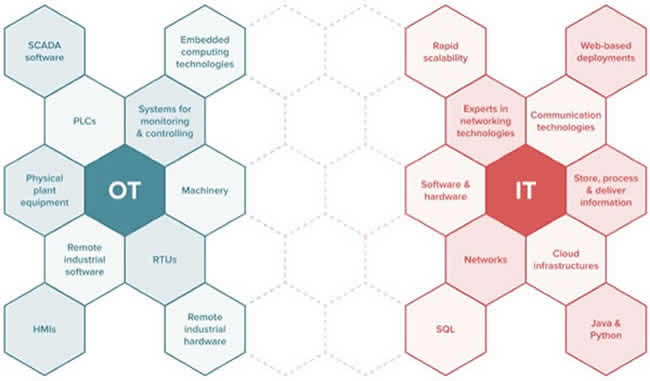
OT has also been defined as technology that interfaces with the physical world and includes Industrial Control Systems (ICS), which in turn includes Supervisory Control and Data Acquisition (SCADA) and Distributed Control Systems (DCS).
Operational technology is everywhere around us: you find it in industrial operations in the smart factory, transportation, oil & gas, mining, in the utility industry (electricity, water….) and in facilities such as office buildings and healthcare facilities to give some examples. OT might be invisible for most; without it the economy and modern way of life wouldn’t be possible.
Originally, OT was mainly a mechanical given. Yet, just like IT, OT evolved through time. In many fields where OT plays an important role, proprietary protocols started to be used and today often still are used. In applications such as building management, communication protocols next started to be used over IP.
An important evolution in OT was the ability to monitor and control physical devices remotely. The injection of IT-based technologies such as big data and machine learning in OT, along with the evolutions in machine-to-machine (M2M) communication and the Internet of Things (sensors), enabled ample innovations with regards to the management of physical devices in industrial processes, among others in diagnostics and maintenance (remote diagnostics, predictive maintenance) and other use cases we know from Industrial IoT.
Whereas operational technology elements once were not connected, today you must look hard to find some that aren’t. Connections and digital technologies are in ever more assets and control devices and systems.
It’s an ongoing trend that will make that in the end we’ll stop talking about operational technology, let alone the differences between IT and OT. The people in operational technology will know about IT in the same way IT people will now about operational technology. Everything digital and connected, with the benefits…and the risks.
Operational technology challenges as the borders with IT blur
IT and OT networks typically were and often still are separated from each other. IT was always the domain of the CIO with a rather strict difference between IT and OT networks but also between the people working in these respective areas. They have different profiles, different types of systems to work with and different tasks/priorities.
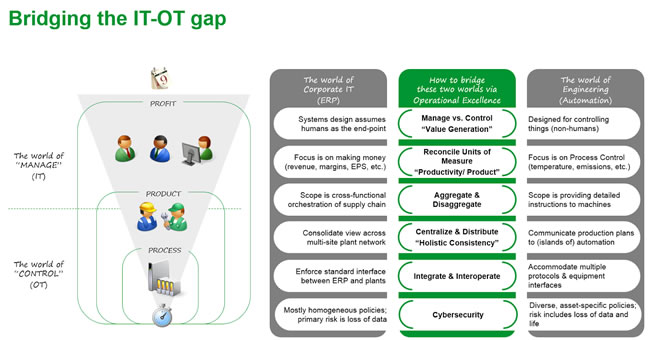
Several years ago, the lines between IT and OT gradually started to blur and the convergence of operational technology and IT is still ongoing. This convergence is not just about technologies but also about the teams and ways of working. With the mentioned IT-based technologies becoming integrated with OT networks and the whole Industry 4.0 and industrial transformation phenomenon, the responsibility over OT is also evolving.
Operational technology is increasingly mentioned from a cybersecurity perspective in these times of industrial transformation. With industrial infrastructures becoming more complex and the ongoing digitization, additional attention is required for OT security. There are also important differences between IT and OT security (without the cyber part). The latter traditionally was more about protecting physical processes, safety, uptime/production/efficiency and protection of people while IT security is more oriented on protecting all aspects of data and how information is stored, transmitted, processed and used in business processes.
With the mentioned convergence, these different priorities and resulting approaches regarding security, often prove to be a challenge now that all these aspects become key. It’s not unusual that there are conflicts between IT and OT when there are computing priorities.
Examples of operational technology, depending on the definition, include the previously mentioned Industrial Control Systems (ICS), key from a security perspective since they are mission-critical. This OT segment is really an umbrella term for various systems to monitor and control industrial processes across a broad range of applications where availability and uptime are key.
Control systems include SCADA systems (Supervisory Control and Data Acquisition), DCS (Distributed Control System) and Programmable Logic Controllers (PLCs). RTUs (Remote Terminal Units), Human-Machine Interfaces (HMI), embedded systems and computing technologies, machinery, physical equipment in plants and Variable Frequency Drives (VFDs) also are operational technologies, as are most connected assets in industrial markets.
PLM Systems, MES applications, Safety Automation Systems, Building Management Systems etc. are often categorized as operational technology too. Operational technology field devices include valves, transmitters, switches and actuators.
More technologies and various types of devices and systems used in operational technology, as well as the usage of operational technology as such, depend on the industry and types of industrial processes.