Manufacturing execution systems (MES) traditionally link ERP (and other business systems) and data flow control and monitoring on the plant floor (operational plant-control systems). How manufacturing execution systems have been and are evolving in the context of smart manufacturing, industrial transformation and end-to-end manufacturing operations management.
Manufacturing execution systems are more critical than ever. The digital plant really is based on data and turning all that collected and aggregated data leads to business value, for instance through better asset, inventory and material tracking, gaining intelligence regarding manufacturing processes for better decision-making, managing performance and quality, coordinating production activities and many evolutions which are still coming our way.
Manufacturing execution systems are evolving information systems and they changed as new technologies such as cloud computing, Big Data (analytics) and IoT (as we know it today in Industrial IoT) emerged.
Then came all those smart machines, new forms of additive manufacturing, next gen robots and cobots, connected objects and smarter sensors, the cyber-physical systems and data approach of Industry 4.0, artificial intelligence, digital twins and new ways of interaction/exchange/collaboration/coordination between data, technologies, people, machines, ecosystems, industrial processes, knowledge and much more. And, so manufacturing execution systems get increasingly connected and “smarter” as well.
Measuring the value and benefits (quantitative and qualitative) gained from Manufacturing Execution Systemusage are more important than ever (ARC Advisory Group)
Everything in the end-to-end industrial environment is becoming smart or intelligent if you prefer although there certainly are also a lot of traditional challenges that remain. Where does this put the Manufacturing Execution System (MES)?
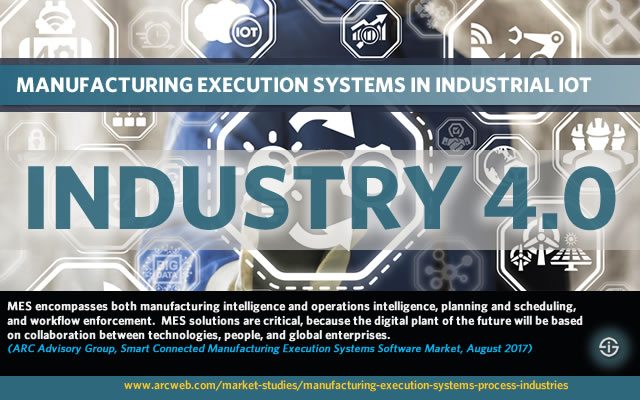
The ‘intelligent’ or ‘smart’ dimension in industrial transformation and Industry 4.0 (mainly Industrial IoT) isn’t just poised to happen on the level of smart products, smart assets and intelligent processes. It’s also key on the level of evolutions regarding programmable logic controllers, industrial control systems (ICS) or process control systems (PCS) overall, SCADA (and SCADA software) and ERP (Enterprise Resource Planning). In fact, it’s key in all applications in and beyond the scope of manufacturing operations management.
We’ve tackled the evolutions from ERP to intelligent ERP before. And we also looked at SCADA systems which are in full flux whereby the near future is easier to forecast than the longer term (intelligent ERP brings us to 2020 and beyond).
With regards to the Manufacturing Execution System (MES), manufacturing operations management (MOM) and product lifecycle management (PLM), to add another one, it’s even harder.
There are those who say that without manufacturing execution systems there simply is no Industry 4.0, while 2) others point to the evolutions in increased intelligence and functionality on the level of process control systems (from distributed control systems to SCADA and PLC) and on the level of Intelligent ERP which will de facto decrease the importance of the MES, 3) still others see the MES as a hub of connectivity and integration, just like building management systems are in smart buildings and, finally, 4) there are those who see MES going away as the traditional automation pyramid de facto is changing and dissapearing (and it’s always been hard to exactly segment all systems and stakeholders in the broad landscape of manufacturing systems).
The place and future of manufacturing execution systems
While the latter is certainly true (bye bye pyramid), before looking at the evolutions, role and landscape of the Manufacturing Execution System it probably isn’t a bad idea to take a step back and look at that good old automation pyramid first.
As mentioned in several other articles with the Manufacturing Execution System we’re traditionally in-between the ERP and SCADA, which in turn sits on the layers of respectively PLC and PID, and the field levels of sensors, actuators, cyber-physical systems, etc.
Manufacturing executives are looking to MES software as an enterprise solution that aligns manufacturing and supply chain technologies (Gartner)
In human language: the MES sits on the operations level, whereas ERP is, well, the enterprise planning level and SCADA and ICS the production level. And what does the MES do in that classic pyramid view? It links with SCADA and ERP for one and it is about aspects such as production planning and scheduling, quality management, workflow enforcement, overall equipment efficiency and overall intelligence regarding the operations AND the production (given the fact it is connected with that level) with a focus on performance and, how else could it be, increasingly analytics and enhanced connectivity with artificial intelligence inevitably being added as a new MES architecture is on the horizon as you’ll read next.
As Industry 4.0 is all about integration (vertical, horizontal…) and given the crucial role of data in Industry 4.0 and Industrial IoT, as well as the impact of IoT, virtually everyone agrees that integrated Manufacturing Execution Systems are key and that we’re moving to platforms, the broader manufacturing operations management (MOM) and/or a service-oriented modular approach as is already offered by several vendors.
From MES functions to MES services
However, it’s in the views of what integration de facto means that the different views on the evolutions of the MES market seem to differ.
If you look at a longer term Industry 4.0 roadmap for the future as it is seen by the people behind the Industrie 4.0 vision and framework you notice a gradual evolution from interoperable standards, interoperable systems, plug-and-work MES (with, among others the Automation Markup Language or AutomationML and OPC UA or OPC Unified Architecture) to MES functions in the cloud, MES functions in embedded systems and self-learning (AI) MES services. In that view a service-oriented modular MES, with functions becoming services, takes center stage, albeit in the broader perspective of MOM and end-to-end visibility and streamlining across the value chain.
Customers in process manufacturing require support to multi-plant enterprise orchestration, easy scalability, optimal interplay with modern technologies and process innovation support through the integration with additive manufacturing, robotics, and PLM systems, etc. (Lorenzo Veronesi, IDC Manufacturing Insights)
Looking at the guiding principles as proposed for that service-oriented MES there is a reference architecture to seamlessly integrate automation and MES with a core of MES functions (or services) and specific functions that can be connected to that core.
Those MES functions do remain needed in Industry 4.0 at all levels, it’s just the architecture of Manufacturing Execution Systems that is strongly changing through Industry 4.0 just as the traditional automation pyramid is changing and dissolving with evolutions in the way in which MES gets embedded and evolves in a service-oriented and soon self-learning approach.
While we look at the future and analysts look at the integration of or support for all the ‘newer’ technologies you can imagine, from big data analytics, and IoT to digital twin simulation applications, augmented reality and so forth as criteria to gauge which manufacturing execution system vendors are leading the pack there is of course also another reality: the non-vendor side where IIoT is far from a fact yet, Industry 4.0 remains a vision for now and manufacturers still work with the same systems they have known.
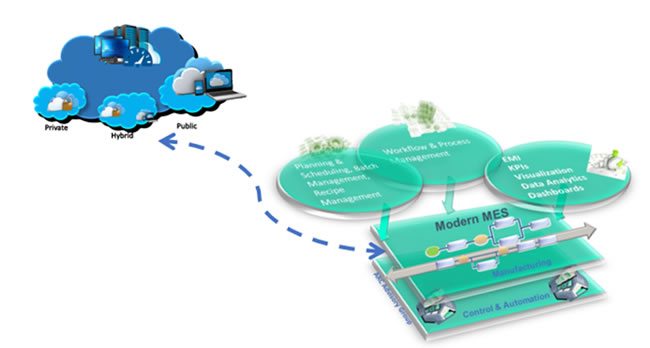
The challenges of manufacturers – selecting manufacturing execution systems software and/or MOM solutions
In order to digitally transform and start the journey of industrial automation it’s clear that a lot still needs to happen on the essential levels of thus far isolated systems that in practice are not integrated and often even very hard to integrate because they date back a long time and really aren’t fit to support changing demands in an easy and affordable way.
The manufacturing execution systems market knows that and while there is an evolution towards a broader and more tightly integrated manufacturing operations management approach the challenges for manufacturers and users of systems in specific verticals remain.
Just as Industry 4.0 is a journey with different steps, the infrastructure, asset and, in this scope, software dimension need to be future fit. In fact, before even deciding on a manufacturing execution system and the modern manufacturing operations management and hyper-connected context in which it fits, it’s best to look at that software stack and not just look at the MES functions/services your Industry 4.0 applications need bit also to take a closer look on the levels of PLC and SCADA, especially since these are in full flux as well.
Digital transformation, Industrie 4.0, and Open Automation Group initiatives are impacting the Manufacturing Execution Systems for Process Industries market (Arc Advisory Group)
The manufacturing execution systems software market
The MES market itself is evolving in different directions and already very differentiated. It is challenged by the ubiquitous need for actionable intelligence and the demands of manufacturers to reduce their cost base while being more efficient and adapting themselves to the changing demands and technologies of Industry 4.0.
When ARC Advisory Group announced its Manufacturing Execution Systems for Process Industries software report, the company stated that MES solutions are critical, because the digital plant of the future will be based on collaboration between technologies, people, and global enterprises.
Among the key new technologies impacting the market are new architectures, predictive analytics, cloud, edge, smart connected devices, virtual reality, and data platforms while improving performance and having process visibility are among the key drivers of the market.
In a blog post ARC’s Janice Abel looked deeper in the evolutions in manufacturing execution systems and the expected continued growth through 2021 with a focus on IoT, connected data, edge computing, advanced analytics and more.
Quote: “While IIoT is a growth factor for MES in some industries, the availability of newer technologies and approaches can hinder MES deployments and other capital purchases. This is partly because some companies are trying to reduce their future risks and understand future directions. They want to acquire a technology that will be part of the new standards, is easy to integrate, easy to use, flexible and can expand and accommodate new technologies and applications as they are developed”.
MOM and MES software solutions and providers
In case you’re in the market for a manufacturing execution software or a manufacturing operations management solution do start from your needs, current situation and roadmap.
Create functional specifications with requirements for your MES in an integrated IT/OT team and look at those use cases you want a (new) MES or MOM solution for (by the way: both are sometimes used interchangeably which is not correct), before looking at vendors, and look at the benefits of an on-premises versus (hybrid) cloud MES deployment for your business.
Identify the challenges at PLC and SCADA level before starting with MES (IDC)
In case you already did that as per usual we added a small list of same MES and MOM vendors and solutions below. Feel free to add more. Warning: several of the solutions and vendors below have been recognized as important ones by analysts in the past few years. Of course that doesn’t mean they serve your needs best.
MES and MOM vendors include are Schneider Electric (Wonderware), Dassault Systemes (Apriso), Oracle, SAP, Siemens, General Electric, Plex Systems and Paper-Less.
In its latest market guide for manufacturing executing system software, Gartner mentions what it calls ‘representative vendors’ such as 42Q, ABB, Applied Materials, Aptean, Ares International, AspenTech, CellFusion, Cogiscan, Critical Manufacturing, Dassault Systèmes,Emerson Process Management, Epicor, Eyelit, Forcam, GE Digital, Greycon, Honeywell Process Solutions, iBASEt, IQMS, iTAC Software, Lighthouse Systems, Mentor Graphics, Miracom, MPDV, Oracle, Performix, Plex Systems, POMS, Prodac, PSI Metals, Rockwell Automation, SAP, Savigent Software, Schneider Electric (among others Wonderware software, now part of the enlarged AVEVA and Schneider Electric industrial software group after the merger), Siemens and Werum IT Solutions.
Manufacturing execution systems are the mainstay of digitalization in the manufacturing sector. In conjunction with the innovative services provided by IoT platforms, they are the bridge for applications that link the real and virtual world of manufacturing (iTAC PR)
For more research and findings regarding the market of MES solutions from Arc Advisory Group and others check out the overview and forecasts. And if you’re looking for more recent MES and MOM solutions reports, as previously mentioned ARC Advisory Group released a MES software report for process industries.
Top image: Shutterstock – Copyright: Panchenko Vladimir – All other images are the property of their respective mentioned owners.