The concept of lights-out automation and lights-out manufacturing or ‘dark manufacturing’ isn’t new and is closely related to more mature stages of Industry 4.0. Several drivers, including the COVID-19 pandemic, accelerate the adoption of lights-out settings, with some industries moving faster to ‘dark factory environments.’
The journey of Industry 4.0 has a staged industrial digital transformation approach with typically four stages. Among the elements in the fourth stage is a further shift to autonomous or semi-autonomous action and machines.
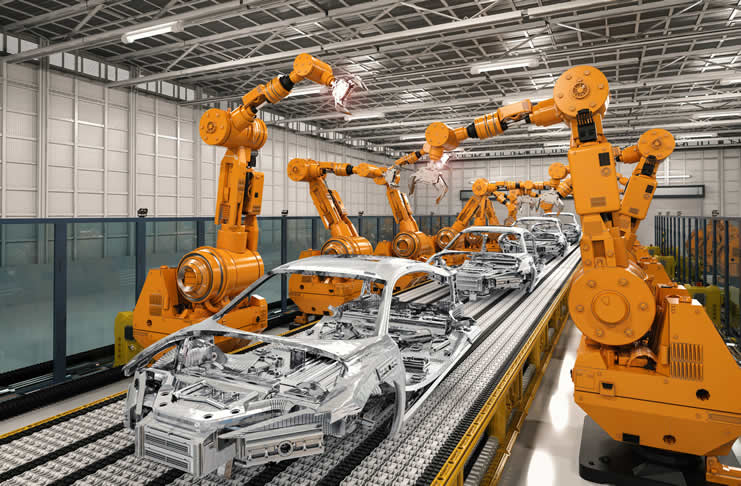
That stage brings us closer to a wholly automated value chain and self-optimizing, autonomous systems, processes, and manufacturing, in other words: autonomy and independence on, among others, the level of operations. The exact same movement towards semi-autonomous or autonomous capabilities, requiring no or little human intervention, is also present in Logistics 4.0.
Lights-out manufacturing and the stages of industrial transformation
It approaches the older dream/vision of lights-out manufacturing in its original meaning (as a methodology or even philosophy). As the name indicates, lights-out manufacturing is about automated, autonomous manufacturing processes with the lights and more (e.g., heating) off since, in theory, extremely little human intervention is needed.
The reality is that we’re entering a situation whereby lights-out environments requiring minimal human intervention come more in reach in some areas and specific cases. There are examples (more below), but there are also failed attempts, and not everyone is convinced.
In a lights-out environment, the manufacturing process is fully automated, with minimal human intervention required to run day-to-day operations.
One could say that the other stages of Industry 4.0, as a vision, pave the way for ‘dark’ environments. You can imagine that without loads of sensors and quite some IoT technologies (and the traditional supporting technologies, connectivity, and systems) lights-out factory setting wouldn’t be possible.
You also need robots (advanced robotics essentially being about autonomous and collaborating industrial robots). Analytics, visualization, and automated decisions based on big data, leveraged in real-time. Artificial intelligence and machine learning, powering the systems, optimization, and other technologies. The vertical and horizontal data integration of Industry 4.0, which is the precondition for nearly full automation, and hard to realize. Digital twins. The list goes on.
Today, most companies have realized projects or pilots in the first stages of the industrial digital transformation we’ve come to know as Industry 4.0. Yet, when a pandemic confronted us with ample manufacturing challenges, accelerated the call for a ‘remote everything’ approach, and increased the pace of automation, lights-out manufacturing experiments and projects come (back) in the picture more too.
If we do get there, it will just not happen without any human intervention and in specific circumstances with specific goals. The idea of factories where all is automated, and people are not needed is fiction and not even desirable. On the contrary, highly skilled people will be required. And even if some of the known and often mentioned examples of lights-out factory projects seem to show it is possible, times are seriously changing.
In several industries, the calls for a different future of work are loud. More and more vendors position novel technologies as ‘human augmentation .’ In some regions, it’s only a matter of time before a technology-centric and automation-centric narrative is replaced by a human-centric. The EU’s adoption of what some started to call Industry 5.0 years ago, an addition to Industry 4.0, is one indicator.
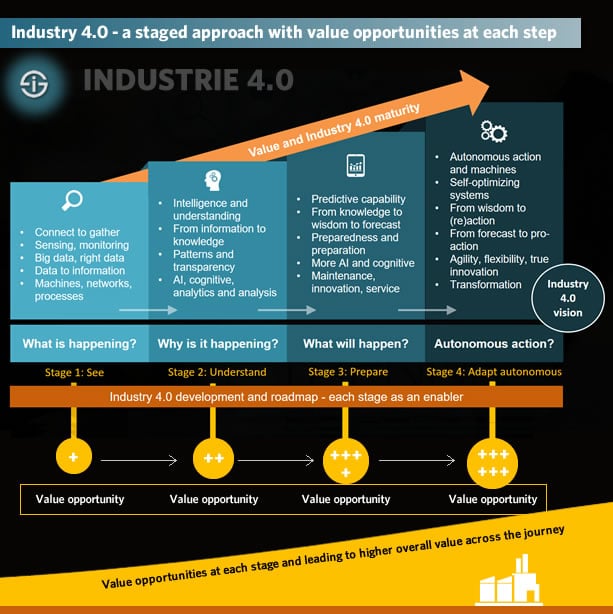
Why lights-out environments could increasingly become a reality
On the other hand, efficiency, cost-savings, and more automation with autonomous elements will remain on the agenda of many. And so will that idea of lights-out manufacturing. It’s just something many don’t prefer to talk about, mainly because of the old idea that you can make factories a machine and ‘lights out’ means no jobs, which isn’t the case.
However, a quick reality check is enough to see that we’re not there yet at all. According to one research firm, only five percent can be called ‘mature’ in adopting Industry 4.0 use cases, realizing significant business gains. Most factories still struggle with paper and manual processes. The integration of IT and OT (short for operational technology) remains a challenge. There’s a lack of ‘connected’ factory workers, automation is still the primary goal (instead of transformation and innovation), and, again, it’s early days in Industry 4.0, in general. Autonomy is only possible in some areas and is not even a goal on its own. And it does require maturity and experience on multiple levels.
Artificial intelligence (AI) will be the most critical tool enabling the lights-out toolkit (Vinay Venkatesan)
Enough thoughts on the matter, however. Time for some facts and details. The reason we’re writing about lights-out manufacturing is an announcement by consulting and research firm Frost & Sullivan. The company announced a new report on transformative trends enabling lights-out manufacturing.
Per Frost & Sullivan, a combination of reasons will accelerate the adoption of light-out settings in smart manufacturing.
These lights-out environment adoption accelerators include:
- the rapidly falling price of robots (on a side note: we also need to emphasize the fast growth of the cobot market where ease of use and flexible advanced cobots attract buyers while the strict separation between robots and cobots disappears),
- continuously increasing labor costs in manufacturing (let’s also not forget the labor shortage and skills gap that exists for some years in some countries in manufacturing),
- classic drivers such as cost savings and increasing production output,
- the need of companies to expand production capacity beyond traditional shift hours, for instance, to take on additional orders and other reasons to ramp up production (remember how the pandemic hindered manufacturing output),
- the need to be more flexible (one can think unexpected production of a-typical goods as during the pandemic here too), more resilient (business resilience being the new holy grail), and shock-proof,
- the opportunities ‘lights out’ offers to innovate and embrace new opportunities and manufacturing approaches, and
- sustainable industry capabilities with energy-saving opportunities during production hours.
There are certainly others. With the pandemic in mind, think about health, for instance. It’s also one of the reasons for the ‘remote everything’ movement, along with resilience. And why would only ‘white-collar’ workers get the possibility to move to some hybrid working model?
In an effort to become more resilient and shock-proof, manufacturers, especially in the West, are compelled to use digital processes to reconfigure their supply chains and move their production lines closer to the point of consumption. This is expected to accelerate the transition to fully automated lights-out manufacturing processes. (Frost & Sullivan)
The industries, technological enablers and opportunities in lights-out manufacturing
Frost & Sullivan reminds that the manufacturing process is fully automated in a lights-out environment with minimal human intervention for day-to-day operations.
The company also stresses that lights-out environments do not intend to eliminate human labor. As is often the case, it has an impact on the type of required factory workers: “a skilled workforce to add value to tasks that require complex problem-solving capability, creativity, and ingenuity.”
Obviously, adopting a lights-out operations model won’t happen simultaneously in all segments and certainly not in all factories. The use case, purpose, and return need to be clear, and many companies don’t have the basics in place. The lack of skills, leadership and differing/evolving priorities all play a role.
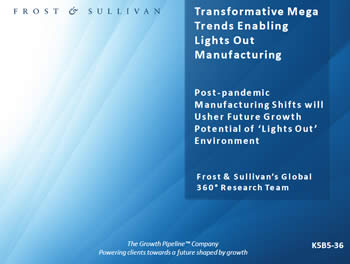
Moreover, certainly initially, the acceleration of the transition to fully automated lights-out manufacturing processes is also more a phenomenon in the West (e.g., labor costs). That’s quite interesting, in fact, since most showcased examples of lights-out factories are in Asia (mainly China).
Existing lights-out factory projects that are often mentioned are frequently realized by companies that aren’t really typical for the manufacturing sector (and never SMEs). Think of the likes of robotics manufacturer FANUC (in Japan), to mention one. Yet, long before that, several attempts of lights-out automation were made.
Many light-out projects in the past also failed (essentially because people turned out to do better than machines and often the reasons for human mistakes were more about processes than workers), so the question is if this time will be different. It’s not that long ago since Elon Musk tweeted that ‘excessive automation at Tesla was a mistake’ and ‘humans are underrated’.
Per Frost & Sullivan, four major segments expected to advance towards a fully automated lights-out environment rapidly are 1) automotive, 2) general manufacturing, 3) electronics and electrical components, and 4) logistics and warehousing.
On a technology level, artificial intelligence is seen as the most critical enabler that will fuel other vital technologies such as robotics, cybersecurity, digital twins, generative design, cloud computing, 5G, and 3D printing.
Vinay Venkatesan, Program Manager, TechVision at Frost & Sullivan, adds that “the manufacturing industry will increasingly rely upon an ecosystem of technology experts, system integrators, and service enablers to achieve agility and customization, with more than 45% of manufacturing applications expected to implement robotics-as-a-service (RaaS) by 2030″.
In the list of lights-out environment adoption accelerators above, we mentioned that Frost & Sullivan states that light-out processes, if everything needed for success and a long-term vision are present, offer new opportunities.
The research firm mentions the following opportunities that a lights-out manufacturing process can unlock:
- the rise of micro-factories in a decentralization model (edge computing does come to mind) with decentralized structures and automated manufacturing processes. Benefits include a smaller workforce, less space needed, energy savings. We would add closer to where consumers and/or supply chain partners are,
- grid manufacturing that essentially enables manufacturers to go for mass customization, one of the other ‘promises’ or dreams of the more advanced Industry 4.0 stages,
- manufacturing-to-zero-as-a-service and seamless IIoT platform information transfers among connected stakeholders, equally in the more mature goals,
- new opportunities regarding condition monitoring and predictive maintenance of all those automated assets ‘lights out’ requires.
Promise or evolution?
It seems the trend, technologies, and will are there. Will it succeed? Again, many have doubts, so time will tell, as will the results of those who join the manufacturers that have done it.
Gartner recommends focusing on lights-out processes instead of lights-out factories. According to Simon Jacobson, investments in smart manufacturing continue to grow, but investments are pivoted towards the worker experience.
While interest in ‘lights out’ manufacturing has re-appeared, the promises of fully automated, hyper adaptable production remain suspect, Jacobson writes in a 2020 article.
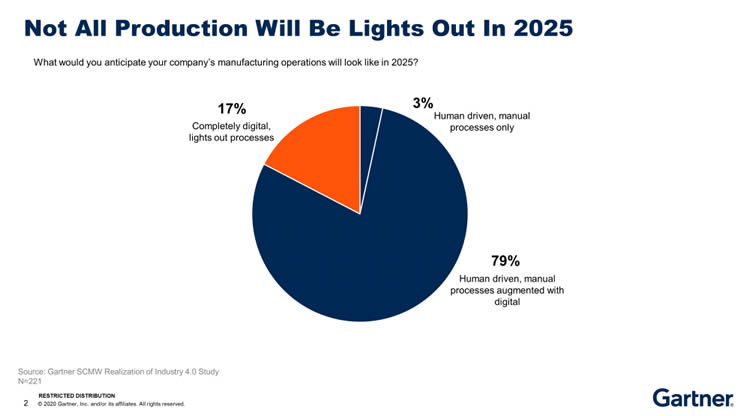
In 2019, 17 percent of respondents to a Gartner survey believed their company’s manufacturing operations would be entirely digital with lights-out processes by 2025. Probably there weren’t too many smaller manufacturers in that survey either.
More thoughts and findings from Frost & Sulivan in the press release of the report, announced in July 2021.
Top image – source: “Frost & Sullivan Reveals How the Lights-Out Setting is Redefining Manufacturing“. All other images belong to their respective mentioned owners and only serve illustration purposes.