As we move to the realization of more Industry 4.0 implementations as part of an ongoing industrial transformation journey, the use of collaborative robots (cobots), which are designed to work alongside people in, among others manufacturing , warehousing, logistics and healthcare, is expected to grow rapidly in the next few years.
Cobots are predominantly used for repetitive tasks whereby intelligent support systems, using cobots, assist the worker.
Recent evolutions regarding both the technologies and the market contribute to this rapid growth. As an example: in April 2017, DHL announced a partnership with Locus Robotics. And it’s not just in the factory or the warehouse. Previously we mentioned how in the digital transformation of healthcare, there is a key role for IoT and for robotics, including cobots.
In our article on the Internet of Things in healthcare we pointed to IDC data. The company expects a 50 percent increase of robots in hospitals for delivery purposes by 2019. And there is more, even in the consumer space (which we don’t cover here).
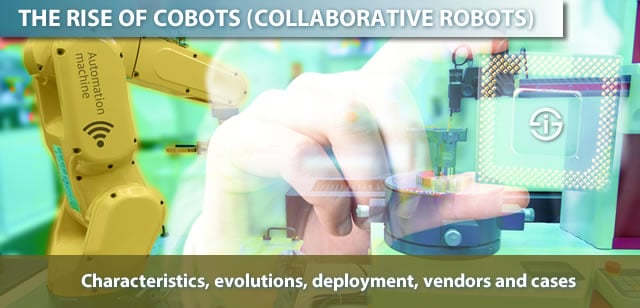
Let’s start with looking at what cobots really are, without a formal definition but by focusing on the key characteristics and some real cases. The idea of cobots nor the use of cobots is new. Yet, usage and developments are accelerating faster than many believe and cobots play a big role in the development of Industry 4.0 and the Industrial Internet of Things.
At the occasion of the Hannover Messe industry fair, you’ll see/hear far more about them, looking at vendor announcements and in 2016 and 2017 they were already omnipresent in Hannover.
What is a collaborative robot or cobot and how is it different from existing industrial robots?
So, what are cobots? As mentioned in the introduction, cobots are collaborative robots. And the collaborative aspects mainly refers to the collaboration between robot and human.
There are plenty of use cases where this provides value, mainly in operations that we can’t – or don’t want to – completely automate. In the example of the collaboration between DHL and logistics cobot expert Locus Robotics, the operation or task is (assisting in) piece picking order fulfilment. In general, cobots are predominantly tested and effectively used for repetitive tasks whereby intelligent support systems using cobots assist the worker, rather than replacing him.
This collaborative aspect obviously is key for the design, possibilities, characteristics and evolutions of cobots.
The diverse challenges in making robots work alongside staff in a secure and valuable way have been gradually solved and we’re at a tipping point whereby there aren’t too many hurdles anymore to leverage them as real-life applications and market evolutions and research show. As mentioned in our article on the usage of robots and cobots in logistics (and the pilot project of DHL), IDC forecasts that already by 2018, a whopping 30 percent of all new deployments of robots will concern smart cobots that operate three times faster and are safe for work around humans.
Cobots versus classic industrial robots: characteristics
Back to the question regarding the “definition of cobots” and, most of all, the difference between cobots and traditional industrial robots.
Can we expect a kind of convergence any time? Probably in some use cases but not now (although industrial robots are evolving too of course) and it all depends on the use case. Below are some (not all) typical characteristics of cobots, in comparison with other industrial robots.
Designed to collaborate
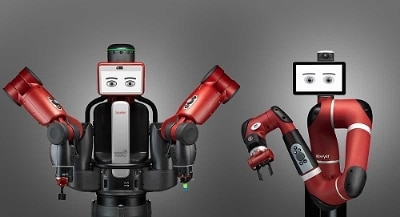
A traditional industrial robot is not designed to collaborate with people. It’s designed to complete a very specific pre-defined task without a need for collaboration within a physical workspace.
They aren’t designed with human safety as a key priority (there are variations); they just need to do their task. Where industrial robots are used, you’ll typically find safety measures and often they are fully caged and shielded from humans on the work floor, e.g. with fences.
Lightweight and movable
A cobot in general is also much more lightweight than an industrial robot, again depending on the type.
That has to do with the typical tasks of cobots, the mentioned safe collaboration aspect and the fact that cobots typically are mobile and/or can be easily moved, which is not the case with your average big industrial robot.
Smart: sensors and more
A cobot is smarter than a classic industrial robot. This doesn’t mean that cobots are more complex and other industrial robots simple.
What it does mean is that cobots are equipped with smart sensors, smart technologies and systems which are linked with the IoT and/or specific systems (for instance, warehouse management systems), depending on the case. Why is this so? Among others because cobots need to safely assist a human being and these smart technologies and sensors are needed to do so (they are typically people-aware, location-aware and context-aware).
If you think about the Industrial Internet of Things in a ‘traditional industrial robots’ context, it’s more often about use cases such as predictive maintenance and the development of new service capabilities for customers as this case from ABB Robotics shows.
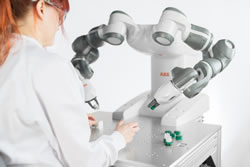
ABB manufacturers ‘traditional’ industrial robots but also cobots. Its ‘robotic co-worker’, YuMi® was introduced at the edition 2015 of the Hannover Messe as a ‘vision for the future. There are certainly ample of cobots out there for various use cases and from various other vendors (we mention some at the end of this article). Yet, the YuMi® infographic at the bottom of this page pretty much sums op how cobots are designed to create benefits in the collaboration between human and smart cobot. Since its ‘launch’, cobot YuMi is being deployed in several business pilot cases and a next generation cobot by ABB, called Roberta, has been announced and showed.
Simpler: ease of use and beyond
A cobot is simpler than most traditional industrial robots. This seems like a contradiction with the previous point but it isn’t.
Cobots are smart in several senses, with context and people (location and movement awareness) as typical characteristics.
Traditional industrial robots can be darn complex but with simple we again need to look at the tasks of cobots: they need to work with people who use them by means of, for instance tablets or tailored devices/display which need to be easy to operate and program. You don’t want a team of highly skilled industrial engineers to do your order picking (which requires totally different skills).
In a next article we look at why the cobot market is poised to boom in 2017 and beyond and more aspects of cobots which you might want to know. They include several market evolutions of which the initiative by DHL is quite an important sign.
Cobots visualized: infographic
Note that on top of these predominantly industrial cobot players, there are plenty of vendors in less industrial markets as cobots indeed are about those and even consumer markets too.
Moreover, an increasing number of industrial giants is making moves into the cobot space. But that’s for another article.
In the meantime and to conclude, below is the promised YuMi infographic by ABB that shows some of the characteristics of the ABB collaborative robot and of cobots in general in a more visual way.

Top image: Shutterstock – Copyright: Zapp2Photo – All other images are the property of their respective mentioned owners.