The manufacturing sector is in the middle of a historic moment in development. With the rise of the IoT, data-centric and interconnected smart factories are quickly becoming the norm. For Industry 4.0 to reach its full potential, however, manufacturers will have to implement edge computing.
Edge computing is the concept of moving computing processes as close to the source of data as possible. Instead of relying on distant data centers, it uses local infrastructure to process data. It takes the cloud and brings it to the hardware that’s already all around you.
Forecasts suggest that there will be 21.5 billion connected IoT devices worldwide by 2025. Imagine if just half of those could run computing tasks for other devices and services. This vast, interconnected computing network would be particularly valuable for smart manufacturing.
Industry 4.0, where it is right now, has some considerable roadblocks hindering its success. Computing at the edge is the solution for getting over many of these obstacles. Here are a few of the most substantial advantages the edge brings to Industry 4.0.
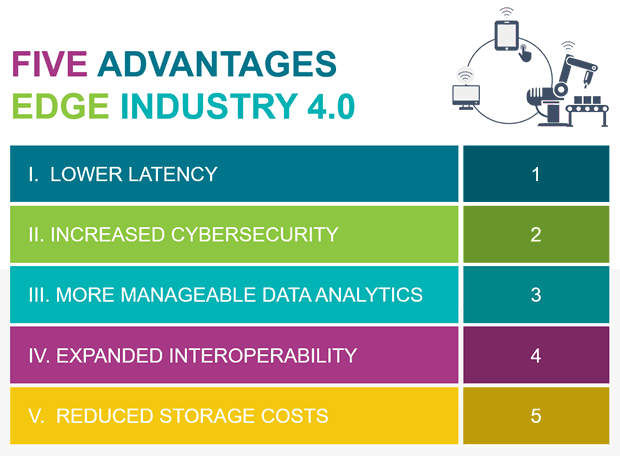
Lower latency
One of the most frequently cited benefits of the edge is its potential to reduce latency drastically. Sending a request to a data center across the world and then waiting for a response to come back takes time. As a result, traditional cloud computing isn’t ideal for many mission-critical applications.
Smart manufacturing without this low latency can’t experience the full benefits of the IoT. If a connected machine on an assembly line recognizes a malfunction, any delay in transmitting that signal could be costly. It could lead to damaged parts or even injury.
Low latency is essential for an interconnected system to work as it should. The nature of traditional cloud computing limits itself in this regard. If most or all industrial computing happened at the source of the data, this wouldn’t be an issue.
Increased cybersecurity
Cybersecurity is, or at least should be, a leading concern for smart factories. As helpful as the IoT is, more devices in the network means more potential entry points for cybercriminals. Securing these networks is a more challenging task without taking advantage of the edge.
The centralized nature of traditional cloud computing makes it vulnerable to hacking, including denial of service attacks. If a factory spread processing and storage functions throughout the edge, however, no single attack could bring down the whole network. Since computing happens closer to the data source, less data is at risk at any given moment.
More than 50% of small and medium-sized businesses have experienced a cyberattack in the last five years. Of these, manufacturing is one of the most frequently targeted industries. Manufacturers interested in data-centric operations need robust cybersecurity, and the edge provides it.
More manageable data analytics
Big data is a foundation of the new industrial revolution. One of the most substantial advantages of the IoT is how it can improve data analytics. Analyzing all of this data requires a considerable amount of storage, bandwidth and computing power, however.
Edge computing alleviates these concerns in two ways. First, it processes data at or near its source, so the overall process is much faster. Second, each data point within the smart factory processes its own information, so no one system has to handle everything.
Processing data at the edge reduces the strain on individual systems, but it also refines the process. Since it’s segmented by nature, it’s easier to sift through and find the most relevant information.
Expanded interoperability
An IoT network is only as effective as it is interoperable. Finding compatible devices or systems can be a barrier to the expansion of smart manufacturing. If these machines could translate protocols, though, they would make themselves more compatible.
Concerns over interoperability are one of the leading barriers to its adoption, since there’s no standard protocol. Moving computing functions to the edge eliminates some of the need for a universal standard. When devices can convert signals themselves, they’ll be able to work with a greater variety of systems.
The edge also serves as a connection point between information and operational technology. It breaks down these distinctions, leading to a more cohesive smart factory.
Reduced storage costs
Smart manufacturing involves a substantial amount of data that requires similarly substantial storage. Traditional local storage options can be inconvenient, and cloud services can be expensive. Storing data at the edge is an ideal middle ground.
With edge storage, factories can choose to send only relevant data to their cloud solutions. The edge can act as a gateway by analyzing data locally and only sending results or summarized data to the cloud. On top of reducing the strain on cloud-based analytics, this helps save on storage costs.
Some edge applications could even save some data locally. They wouldn’t need to store much, since each machine would only handle its own operational data. The result is a segmented, organized and affordable data storage solution.
The future of Industry 4.0 depends on edge computing
Industry 4.0 can only get so far without transitioning to the edge. If the IoT was the computing step after the cloud, the edge is the next logical step after the IoT. Without adopting this technology, Industry 4.0 won’t be able to progress to its full abilities.
This transition won’t and can’t happen overnight, but it’s all but inevitable. How fast the manufacturing sector can step into the next age of industry depends on how fast it can implement the edge. Until that happens, the industrial IoT can’t unlock its full potential.
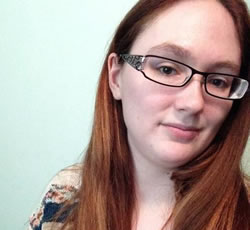
Article by Megan R. Nichols
Megan R. Nichols is a technical writer and the editor of Schooled By Science. She regularly discusses Industry 4.0 for IoT Times, ReadWrite and IoT Evolution. When she isn’t writing, Megan enjoys hiking local trails. For more articles follow Megan on Twitter.