The technologies that are typically associated with Industry 4.0 and digital transformation in manufacturing probably need no more introduction: cloud computing, (big) data, the Internet of Things, robotics, more than ever, artificial intelligence, and the rest of the so-called third platform and various digitization and digitalization enablers.
The increasing integration of several of these technologies, such as AI and robotics, enables new possibilities and continues to transform the market compared to when Industry 4.0 was launched as a concept.
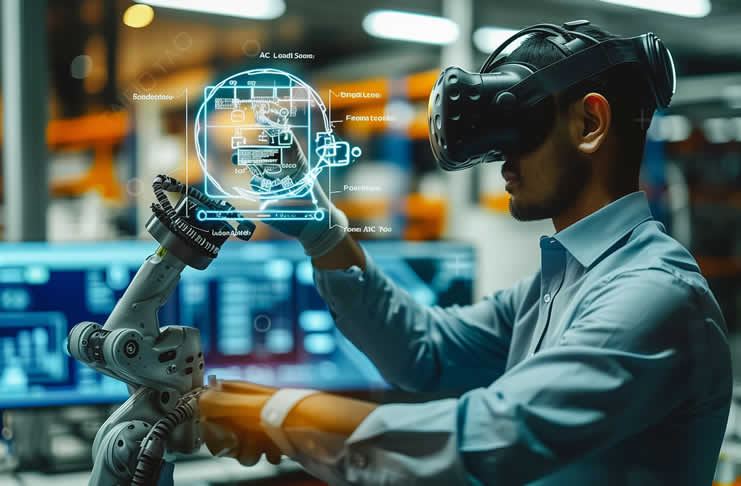
AI and robotics are increasingly shaping manufacturing operations and the activities of ample verticals across numerous types of applications as tech and AI players come up with new possibilities to do so. As Jensen Huang, CEO of NVIDIA, stated at COMPUTEX 2024, “the next wave of AI is here. Robotics, powered by physical AI, will revolutionize industries”. Say hi to physical AI and AI robots on an increasing scale across sectors and use cases.
“Eyes, hands, brains and mobility” – AI and robotics beyond 2025
In March 2025, Google, introduced new AI models designed for robotics applications, including Gemini Robotics (its “Gemini 2.0-based model designed for robotics”) and Gemini Robotics-ER, “a Gemini model with advanced spatial understanding”. This is not Google’s first foray into AI-driven robotics but it’s another important step and a challenge to the competition.
The two AI models should take robots’ capabilities beyond what we know on a larger scale. They allow robots to see the digital environment, understand instructions, and take action. Gemini Robotics is an advanced vision-language-action (VLA) model based on Gemini 2.0, where the output consists of physical actions—the technical and other aspects in detail in this paper by the Gemini Robotics Team.
The next wave of AI is here. Robotics, powered by physical AI, will revolutionize industries (Jensen Huang, CEO of NVIDIA)
Robotics companies have also been advancing AI-driven robotics. Companies such as ABB, Fanuc, and KUKA are integrating AI into their industrial robotic systems.
Per ABB, “2025 marks the beginning of a new era of AI application in Industrial robotics,” whereby the company welcomes a new age of Generative AI-powered automation that makes robots even more intelligent, accessible, and versatile, disrupting new and emerging sectors for robotics.” On the occasion of launching a new brand film celebrating the company’s 50 years of robotics leadership, ABB states that eyes, hands, brains, and mobility will define robotics beyond 2025.
When asked about the trends that will shape 2025 in terms of industrial digitalization, Quirin Görz, CEO of KUKA Digital, stated that the automation industry would be characterized by transformation in the next few years, with primarily “the data economy, everything to do with simulation and virtual commissioning and, of course, artificial intelligence.” At the top of his trend list is the digital twin.
As manufacturers adopt AI-driven robotics, efficiency, scalability, and cost-effectiveness are obviously central considerations. Yet, there is more.
The global market value of industrial robot installations has reached an all-time high of US$ 16.5 billion. Future demand will be driven by a number of technological innovations, market forces and new fields of business as the trend towards artificial intelligence in robotics is growing (International Federation of Robotics)
The convergence of AI and robotics (and other smart technologies)
In the early years of the Industry 4.0 model (and the Industry 5.0 view), manufacturing focused primarily on automation, interconnectivity through technologies such as Industrial IoT, cyber-physical systems, data exchange, and cloud.
While robotics played a key role, its integration was often mainly limited to pre-programmed, repetitive tasks. Lately, the convergence of AI, robotics, and advanced computing technologies has expanded the capabilities of smart manufacturing systems, with the move from static automation to adaptive, AI-driven decision-making being a vital shift. Traditional Industry 4.0 approaches relied on fixed algorithms and rule-based systems to manage production, whereas AI-powered robotics now enable dynamic responses to real-time data. With the integration of AI, robotics can adjust manufacturing processes autonomously.
Another significant development is the fusion of AI, robotics, and digital twins. As we saw before, digital twin technology has become an essential component in smart manufacturing and is high on the industry list for 2025. AI-powered robotics utilize digital twins to simulate, predict, and refine manufacturing operations before implementing changes on the factory floor.
Additionally, AI-driven robotics are increasingly integrated with edge computing and IoT networks, enabling decentralized decision-making at the edge or the production level. Unlike traditional centralized automation systems, edge AI allows robots to process data locally, reducing latency and improving responsiveness. This advancement is particularly beneficial in high-speed production lines and customized manufacturing, where real-time adaptability is crucial.
“The most significant come driver of the physical AI market comes from advancements in AI allowing robots to see, to learn, to move, to talk, to take instruction into code and then actions. Only recently has multi-modal AI allowed all these elements to fit together. AI in turn is becoming embodied and physical. In parallel have been advancements in dexterity. Some robots can now thread a needle or suture a kernel of corn. Robots are on the move, from theory to reality and from useless to useful.” (The Rise of AI Robots, Physical AI is Coming for You – Citi GPS: Global Perspectives & Solutions, December 2024)
The role of robotics obviously goes beyond assembly lines and encompasses logistics, maintenance, and workforce augmentation for quite some years now. AI-powered robots can collaborate with human workers more seamlessly, assisting in precision tasks, inventory management, and autonomous inspections, to mention a few. The development of self-learning, agentic AI-driven robots will enhance these capabilities, allowing systems to evolve and improve over time without requiring extensive reprogramming.
As AI and robotics continue to evolve, their integration within the industrial digital transformation framework is shifting manufacturing toward a more interconnected, autonomous, and intelligent ecosystem. The future of smart manufacturing will likely involve even deeper AI-driven analytics, improved robotic autonomy, and further integration with blockchain and cybersecurity frameworks to ensure secure and efficient production environments.
One of the most significant impacts of AI in industrial robotics is predictive maintenance. AI-enabled robots analyze vast amounts of operational data to detect early signs of mechanical wear and potential failures. As you know, the aim of this predictive approach is to enhance efficiency, reduce downtime, and minimize errors, leading to more significant cost savings.
AI also enhances robotic perception, allowing robots to handle complex tasks such as precision assembly, welding, and material handling with minimal human oversight.
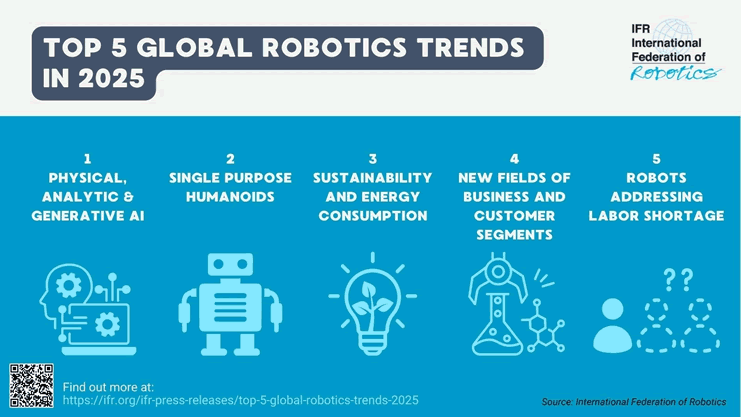
Evolving role of collaborative robotics in manufacturing
Collaborative robots, or cobots, have undergone significant advancements due to the integration of artificial intelligence as well. Unlike traditional industrial robots, which operate in isolated environments, cobots are designed to work alongside human workers.
Recent developments in AI have significantly enhanced cobot capabilities. Machine learning algorithms now enable them to learn from human behavior, improving their ability to anticipate actions and respond in real-time.
This has led to more effective human-robot collaboration in manufacturing environments, reducing the need for manual programming and increasing productivity. AI-driven cobots are also equipped with enhanced perception systems, such as computer vision and sensor fusion, allowing them to dynamically recognize and adjust to changing environments.
With AI continuing to drive innovation in collaborative robotics, the role of cobots in manufacturing is expected to expand further. They will increasingly function as proactive partners.
AI and robotics: a look at GenAI and agentic AI
Looking at the key global robotic trends overall, it’s clear that AI will continue to play an increasing role in robotics in 2025 as well.
Per the Top 5 Global Robotics Trends 2025, artificial intelligence (physical, analytical, and generative AI) ranks as the number one trend.
While analytical AI enables the processing and analyzing of large amounts of data collected by the sensors, physical AI allows robots to train themselves in virtual environments, operating by experience rather than programming.
Talking about AI and robotics trends, it’s almost inevitable to take a brief look at the forms of AI that generate the most buzz these days: generative AI or GenAI, and in the longer term with an eye on the future: agentic AI.
Generative AI in industrial robotics
Per the International Federation of Robotics, Generative AI projects aim to create a “ChatGPT moment” for Physical AI. This AI-driven robotics simulation technology will advance in traditional industrial environments and service robotics applications.
Generative AI influences industrial robotics by enabling greater flexibility, problem-solving capabilities, and adaptability in manufacturing environments. Unlike traditional AI models that rely on fixed datasets and rule-based operations, generative AI can simulate and optimize processes dynamically.
One of the most significant applications of generative AI in manufacturing is in robotic process planning.
Another role of generative AI is in predictive learning and autonomous adaptation. Robots with generative AI can analyze their performance, identify inefficiencies, and autonomously improve over time.
Robot and chip manufacturers recently are investing in the development of dedicated hardware and software that simulate real-world environments. This so-called Physical AI allows robots to train themselves in virtual environments and operate by experience, rather than programming. (International Federation of Robotics)
Agentic AI and the future of robotics in manufacturing
The next big trend in AI that virtually everyone is talking about is Agentic AI. It is believed to represent a new stage in the evolution of AI-driven robotics, enabling machines to operate with more autonomy and strategic decision-making capabilities.
Unlike traditional AI models that execute predefined instructions, agentic AI allows robots to assess situations, set goals, and perform complex tasks independently, reducing the need for human intervention.
One of the key applications of agentic AI in manufacturing is adaptive automation. AI-powered robots with agentic models can dynamically reconfigure production lines in response to changing demand, material shortages, or machine failures.
Additionally, agentic AI is also advancing predictive maintenance. Robots embedded with these AI models can monitor their operational health, predict potential failures, and autonomously schedule maintenance before disruptions occur. This proactive approach is already being implemented in industrial robotics used in heavy machinery manufacturing.