In 2011, five years after being tasked to develop a new high-tech innovation strategy for Germany, the special working group for innovation policy came up with its recommendations for what has become known as Industry 4.0.
The vision and concept of Industry 4.0, along with its cyber-physical systems and Industrial IoT, went quickly global, and the German initiative joined forces with similar ones in other countries (e.g., the Industrial Internet, mainly known back then in the US).
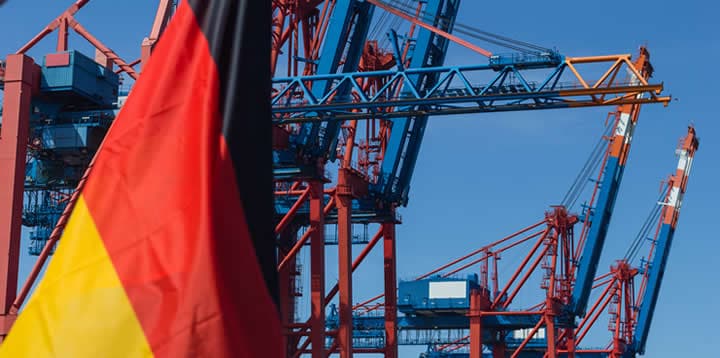
In all these visions, there was a central role for Industrial IoT, one could say the ‘industrial version’ of the Internet of Things, although many use the term Industrial IoT as a synonym of Industry 4.0 nowadays.
Today, 21 years later, the state of Industrial IoT in Germany, the native country of the Industrie 4.0 vision, doesn’t look very rosy. Against the backdrop of the end of the global health pandemic and the geopolitical hard times, the adoption of Industrial IoT in the German industry is stagnating at a low level, according to IDC.
29 percent of German industrial companies are actively implementing IIoT projects (IDC, April 2022)
German industry remains on the Industrial IoT sidelines: data
Less than two months before the annual Industry 4.0 fair, Hannover Messe, where Industry 4.0 was once officially presented, IDC points out that – how else could it be – the German industry is in crisis mode and strongly focuses on stability and resilience.
The list is endless: the overall economic situation, the Ukraine war, and the supply chain problems that started during the COVID-19 crisis are certainly not unique to Germany alone.
And it probably isn’t a surprise that the mindset is not exactly one of innovation, a high appetite for risk, and room for advanced digital transformation.
According to IDC, operational metrics such as profit and costs (40 percent), productivity (38 percent), and customer loyalty (29 percent) are top of mind for the business side of the German industry, while the operational side of industrial companies focuses on continuity in production (29 percent), cutting energy and resource costs (28 percent) and reducing rejection rates (26 percent).
However, these goals could have been achieved more easily if the German industry had moved faster in becoming more flexible to crises, more agile, and more data-driven by adopting IIoT and a data-centric culture, per IDC.
This wouldn’t just have helped them meet the goals they value most now but also would have enabled them to go further than responding to all these short-term changes with new data-based products, services, and business models. Innovate and tap into new revenues indeed.
IDC still sees opportunities ahead for German industrial companies
While IDC surveyed 250 industrial and industry-related companies with more than 100 employees in Germany in January and February 2022 on Industrial IoT to arrive at these sobering German results, it’s pretty clear that Germany isn’t the only country where organizations missed quite some opportunities. Moving faster instead of remaining on the sidelines, as all too many still do – in Germany as well – might have made a significant difference indeed.
According to IDC, 20 percent of German industrial companies are still in the research stage when it comes to Industrial IoT. Another 30 percent is ‘evaluating,’ and 20 percent is planning.
Despite all the crises in past years, this is definitely not what the industry wanted to see, let alone once promised to realize.
This year’s Hannover Messe theme is “Let’s create the industry of tomorrow.” It’s a theme one can repeat each year. Yet, at some point, one needs to take action. As IDC puts it, by failing to adapt, more than a few companies may have slept through the best opportunity to better respond to risks and problems in supply and value chains. However, the company adds that it is not too late for a turnaround—more about that – in German – here.